We'd like to remind Forumites to please avoid political debate on the Forum... Read More »
[Solved] Techie question about tin cans.
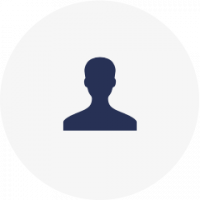

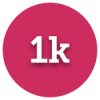
Comments
-
I am no expert on can making but in my view it has more to do with the impurities that could potentially be present in recycled steel which make it unsuitable for food grade packaging. The issue will be more to do with verifying the source of the recycled material rather than the recycling process itself. It's also unlikely that recycled steel (when recycled properly of course) is more susceptible to rusting or is less suitable for thinner cans.
A quick Google search verifies what I have said above.
Like I say I am no expert in steel but I do have some experience in recycling food grade packaging materials.1 -
Hi El_TorroThanks for your reply.I hadn't thought about the impurities.With Blast Furnaces the temperature is extremely high.So probably any nasties will be vaporized.Maybe EAFs don't get hot enough to kill *everything*.Never interrupt your enemy when he is making a mistake.0
-
bat999 said:Hi El_TorroThanks for your reply.I hadn't thought about the impurities.With Blast Furnaces the temperature is extremely high.So probably any nasties will be vaporized.Maybe EAFs don't get hot enough to kill *everything*.4
-
In the UK there doesn’t seem to be any issue in using “recycled” steel. See https://www.mpma.org.uk/information/
and cans are coated on the inside anyway.2 -
Hi PHKGood find that mpma site.Maybe they have more strict food packaging rules in US than in UK/EU, but I would have expected the opposite.
I think we coat insides of aluminium cans to hide metallic taste when drinking, wasn't aware they did it with steel cans too.mpma site says..."For many food and drinks cans it is necessary to coat the metal with an organic material to prevent chemical actions occurring between the metal of the container and the product or the external environment."Never interrupt your enemy when he is making a mistake.0 -
bat999 said:Hi PHKGood find that mpma site.Maybe they have more strict food packaging rules in US than in UK/EU, but I would have expected the opposite.
I think we coat insides of aluminium cans to hide metallic taste when drinking, wasn't aware they did it with steel cans too.mpma site says..."For many food and drinks cans it is necessary to coat the metal with an organic material to prevent chemical actions occurring between the metal of the container and the product or the external environment."
Aluminium "tin" cans are more recent but also need coating on the inside at least. However I think it is possible for some purposes to use a type of synthetic coating.0 -
US has lower food standards - Hence most of their food being banned for export.
But as far as I know, food cans in the UK and EU are required by law to be "food safe" meaning they have to be coated to prevent any contamination of the food by packaging.
https://www.food.gov.uk/about-us/key-regulations0 -
The coating is the reason you shouldn't buy badly dented cans on the reduced shelf. If the inner coating is breached, the food can become contaminated , and spoil. Probably won't kill you though.0
-
I asked a certain Google Gemini and it said as follows:
spearheaded by extensive research and insights from industry experts, the preference for virgin steel in the production of tin cans is rooted in the material's specific metallurgical properties, which are crucial for the demanding requirements of food packaging. While recycled steel from Electric Arc Furnaces (EAFs) is a cornerstone of sustainable steel production, its chemical composition presents challenges for the unique application of tinplate.
The primary reason for this preference lies in the presence of "tramp elements" in recycled steel. EAFs primarily process scrap steel, which can contain a variety of other metals such as copper, nickel, and tin. These elements are difficult and costly to remove during the recycling process. While present in minute quantities, these tramp elements can significantly impact the formability and corrosion resistance of the ultra-thin steel sheets required for tin cans.
For instance, an excess of copper can lead to embrittlement of the steel, making it more prone to cracking during the can-forming process. This is particularly critical as tin cans are manufactured through a highly demanding drawing and ironing process that stretches the steel to its limits. Any inconsistencies or weaknesses in the steel can result in production line failures and, more importantly, compromise the integrity of the final container.
Furthermore, the presence of these tramp elements can interfere with the uniform application and adhesion of the protective tin coating. This can create microscopic points of weakness where corrosion can initiate, potentially leading to rust and, in a worst-case scenario, compromising the safety of the food within the can. Virgin steel, produced in a blast furnace from iron ore, has a much more controlled and consistent chemical composition, with significantly lower levels of these detrimental tramp elements. This inherent purity makes it the ideal substrate for producing the high-quality, ultra-thin, and highly formable tinplate required for food and beverage cans.
It is not that recycled steel is inherently inferior, but rather that its typical composition is less suited for this very specific and demanding application. The steel used for tin cans must be exceptionally clean and possess a precise chemical makeup to be successfully drawn into a seamless can body and to ensure the long-term safety and stability of the packaged food. While advancements in steel recycling and purification are ongoing, for now, the consistency and purity of virgin steel from blast furnaces remain the industry standard for safeguarding the quality and safety of tinned goods.
The Surprising Purity Demands of the Humble Tin Can: Why Virgin Steel Has Reigned Supreme
For decades, the steel used to make the tin cans that line our pantry shelves has been almost exclusively "virgin" steel, produced in traditional blast furnaces. This has been a surprising reality for many, given the strong emphasis on recycling in the modern era. The preference for new steel over recycled material from Electric Arc Furnaces (EAFs) stems from the incredibly high-quality demands of can manufacturing, where even minute impurities can have significant consequences.
Your surprise is well-founded, and your intuition points to the core of the issue. The primary reason for the historical reliance on virgin steel for tin cans lies in the detrimental effects of "tramp elements" present in recycled steel scrap. These residual metals, most notably copper, can compromise the integrity of the final product in ways that are critical for food safety and the can manufacturing process.
The Problem with "Tramp Elements"
Electric Arc Furnaces primarily use scrap steel as their raw material. While this is an excellent way to recycle and reduce the environmental footprint of steel production, it introduces a host of other elements that are difficult and costly to remove. These tramp elements, which also include tin, nickel, and molybdenum, become co-mingled in the molten steel.
The most significant challenge for tinplate production—the material of tin cans—comes from copper. Even in small concentrations, copper can cause a phenomenon known as "hot shortness." During the hot rolling process, where steel is thinned at high temperatures, copper can create a low-melting-point liquid phase at the grain boundaries of the steel. This leads to surface cracks and defects. For a product as thin and as stressed as a food can, such imperfections are unacceptable. They can compromise the structural integrity of the can and create potential sites for corrosion, which could be harmful.
Furthermore, these tramp elements can negatively impact the steel's formability. Modern two-piece food cans are a marvel of engineering, formed through a process called "drawing and ironing" (DWI). This process involves drawing a circular steel blank into a cup and then ironing the walls to make them extremely thin, all without tearing or wrinkling. The presence of impurities can reduce the steel's ductility, making it more prone to failure during this demanding forming process.
The Quest for Ultra-Thin, Flawless Steel
The need for ultrathin steel for cans is driven by a desire to reduce material usage, cost, and weight. However, as the steel gets thinner, the impact of any defects becomes more pronounced. A microscopic crack that might be insignificant in a thick steel beam could be a catastrophic failure point in a can wall that is only a fraction of a millimeter thick. This is a key reason why the pristine quality of virgin steel, with its tightly controlled chemical composition, has been the standard for so long.
A Greener Future for the Tin Can
The good news is that the steel industry is on the cusp of a major shift. The significant energy savings and lower carbon emissions associated with EAFs are powerful incentives to overcome the challenges of using recycled steel for high-quality applications.
Companies like Tata Steel are investing heavily in advanced EAF technology and sophisticated scrap sorting and processing systems. The strategy involves a two-pronged approach:
- Better Scrap Management: Implementing more rigorous sorting of scrap to separate higher quality, less contaminated steel.
- Dilution with Virgin Iron: Mixing the molten scrap in the EAF with a proportion of new iron, such as Direct Reduced Iron (DRI) or pig iron. This dilutes the concentration of tramp elements to a level where they no longer compromise the steel's quality for demanding applications like tinplate.
Tata Steel UK, for instance, has announced plans to produce high-grade packaging steel using EAF technology, with trials expected to begin in the coming years. This move signals a significant technological advancement and a commitment to a more circular economy for steel packaging.
In conclusion, while it may seem counterintuitive, the humble tin can has historically required steel of a higher purity than many other applications. The exacting demands of the can manufacturing process and the critical importance of food safety have made virgin steel the material of choice. However, as technology evolves, the industry is poised to increasingly incorporate recycled steel into the production of the cans that are a staple in our kitchens, bringing the environmental benefits of recycling to this essential packaging.
1
Confirm your email address to Create Threads and Reply
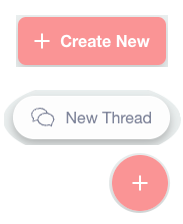
Categories
- All Categories
- 350.8K Banking & Borrowing
- 253K Reduce Debt & Boost Income
- 453.5K Spending & Discounts
- 243.8K Work, Benefits & Business
- 598.6K Mortgages, Homes & Bills
- 176.8K Life & Family
- 257.1K Travel & Transport
- 1.5M Hobbies & Leisure
- 16.1K Discuss & Feedback
- 37.6K Read-Only Boards