We'd like to remind Forumites to please avoid political debate on the Forum... Read More »
We're aware that some users are experiencing technical issues which the team are working to resolve. See the Community Noticeboard for more info. Thank you for your patience.
📨 Have you signed up to the Forum's new Email Digest yet? Get a selection of trending threads sent straight to your inbox daily, weekly or monthly!
Screw help needed please
Options
Comments
-
I used one of those screw extractors a couple of months ago and, after a bit of cursing, trying different sizes, it eventually worked!One other thing which might help is some heat to make the metal expand/shrink to help "un-stick" it.This video shows some options (the rubber band one is something I hadn't thought of!).In my case the extractor tool included a drill bit to make a pilot hole.
0 -
GDB2222 said:Bendy_House said:eBay has packs of 10 screws for £3. Good chance the replacement cartridge will come from there too.
Daisy, you HAVE turned the water off to that tap, haven't you?I'd imagine so.I'd hope so...1 -
Daisy_84 said:Apodemus said:I suspect screw extractors work best in the hands of those with sufficient DIY experience to not have stripped that screw in the first place! Drilling out the screw head may be the best solution, although you can sometimes cut a new slot with a Dremel. That screw might also need some heat to help free it. But getting heat or a Dremel in there without other collateral damage may be impossible.I’ve become so used to doing my DIY. I replaced my bathroom extractor myself earlier in the year.I also replaced by shower taps myself last year. I didn’t realise that kitchen sink taps would be so tightly screwed that I’d end up destroying there screw.
I’d rather replace the washer myself if possible, rather than pay British Gas £60 excess to come fix it (I have a contract with them). And no I won’t use a local plumber. The last time I used a local plumber he charged me £75 for a shoddy job.1 -
grumbler said:... hammering a new hard screwdriver bit (not impact one, they are soft) into the damaged slot.0
-
Apodemus said:grumbler said:... hammering a new hard screwdriver bit (not impact one, they are soft) into the damaged slot.All decent screwdrivers will have 'hardened' tips, so that they don't easily deform in use. This will also make them slightly brittle, but I wouldn't worry about that in this case - you aren't using it as a chisel (that comes later in your DIY career...)So, yes, the screwdriver tip will be much harder than the brass screw, so should re-shape the damage to some degree, and also hopefully break the 'seal' betwixt the screw's thread and the tap's body.I think what Grumb means about impact driver bits is that they cannot be TOO 'hard' because that will also mean too 'brittle' - so they'd break up in use. He doesn't mean 'soft', just not well-'ard. They've been 'annealed' and 'tempered' and stuff.You can firmly tap your screwdriver into place with confidence. Keep it in a direct straight line into the screw head.And good squeeze clockwise first, then undo anti.And then get out the drill... :-)1
-
Apodemus said:grumbler said:... hammering a new hard screwdriver bit (not impact one, they are soft) into the damaged slot.Usually they are, otherwise this wouldn't work. Some special screws are hardened and you cannot even drill them.or that an impact screwdriver bit is softer than a normal one?ThisIf the latter, then that seems counter-intuitiveNope. Harder materials are usually more brittle and this applies to steel too. Hard impact drill bits would break from strong torsion impacts.
1 -
grumbler said:Apodemus said:grumbler said:... hammering a new hard screwdriver bit (not impact one, they are soft) into the damaged slot.Usually they are, otherwise this wouldn't work. Some special screws are hardened and you cannot even drill them.or that an impact screwdriver bit is softer than a normal one?ThisIf the latter, then that seems counter-intuitiveNope. Harder materials are usually more brittle and this applies to steel too. Hard impact drill bits would break from strong torsion impacts.0
-
-
The thinner shank on the impact bits is to do will taking some of the stress away from the tip.2
-
Bendy_House said:Is your screwdriver in good condition, Daisy?
If the edges of the (presumably) PZ2 tip aren't nice and defined, then it may be worth treating yourself to a new set, especially as you are up for DIYing such jobs.
Place the screwdriver in position, and gently-firmly give the handle a series of taps in order to drive the tip in a fraction more, and to hopefully tidy up the mangled part a wee bit. Brass - the screw material (so it doesn't rust) - is a lot softer than the (presumably) 'hardened' tip of the screwdriver, so should slightly reform the 'slot'. Also, such taps might help to loosen - 'break the seal' around the screw thread. So try that first.
Then, both hands on the 'driver, firm grip, try and keep it steady - straight line in to the screw - push it in firmly, and undo anti-clock as normal (very unlikely to be a LH thread).
Does your screwdriver shaft or handle have a 'hex' part designed to take a spanner to help turn it? If it does, and you have the tools, then the ideal way would be to add this spanner to the shaft, and then use one hand to press the 'driver in firmly, and the other turns the spanner - that way the 'driver doesn't wobble, which is what often causes screw heads to be mangled.
If that fails, get your drill and fit a bit sized smaller that the screw head, but larger than the screw thread - so 5mm-ish? Nice sharp example. Now hold the drill in both hands, with one supporting the drill shaft as close to the chuck as possible, and with the back/side of that hand then being supported by the sink top - place something under your hand to raise it to the exact required height if possible. The idea is to have the drill body under FIRM control so it doesn't wobble.
Now fire up the drill at a fair rate, and SLOWLY - and holding the drill firmly in control - bring the drill tip into GENTLE contact with the centre of the screw head. You will likely find that the drill will 'shudder' slightly as it first makes contact with the uneven screw head, so anticipate this. Even watch for it trying to 'jump' out of this first contact - hold firmly! Slow first contact.
The drill will then start to cut the V in to the head's centre. Once it's gone deep enough - 5mm-ish - the head should just pop off. Very satisfying.
Pull off handle - it could be tight on the splines - and gently use grips to unscrew the remaining screw shaft.
Add a new screw to your shopping list.
It'll take less time to do than read0
Confirm your email address to Create Threads and Reply
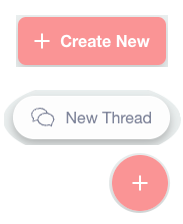
Categories
- All Categories
- 350.8K Banking & Borrowing
- 253.1K Reduce Debt & Boost Income
- 453.5K Spending & Discounts
- 243.8K Work, Benefits & Business
- 598.7K Mortgages, Homes & Bills
- 176.8K Life & Family
- 257.1K Travel & Transport
- 1.5M Hobbies & Leisure
- 16.1K Discuss & Feedback
- 37.6K Read-Only Boards