We'd like to remind Forumites to please avoid political debate on the Forum... Read More »
📨 Have you signed up to the Forum's new Email Digest yet? Get a selection of trending threads sent straight to your inbox daily, weekly or monthly!
No plug socket behind washing machine
Options
Comments
-
Bendy_House said:Section62 said:You mean having dragged the heavy washing machine out of the way to get access to the plug/socket....Rather than simply turning the power off at the (double pole) FSU?I mean if the OP wished to remove their W/M, or replace it. Will they need a sparky each time? (Assuming - I think reasonably - that they are not keen to wire into that outlet plate themselves.)Ah, I thought by 'very quickly' you meant in an emergency.It depends how you see the issue. From a tenant's point of view being able to plug their washing machine in would definitely be an advantage, but as we've seen from this discussion, give someone a 13A socket and sooner or later they will plug something into it which they shouldn't.Not having a 13A socket discourages casual use of that electrical point for anything other than its intended use.I can see why a building owner or landlord would be happy to do something which acts as a barrier to an occupant doing something they shouldn't do.There's also another advantage to not having a plug and socket behind the washing machine - it means there won't be a fuse in a relatively inaccessible location that may need checking/replacing. Having the (only) appliance fuse in a FSU above the worktop makes it easier to check/change, and avoids the situation of the occupant changing the fuse in the FSU and not realising there is another (hidden) one behind the washing machine.grumbler said:Section62 said:
Why would that be "much better"?Because- There will be no need to add a plug back when the OP moves to another accommodation
- The new tenants won't need to cut their plug and call an electrician to hardwire their WM.
Yes, it's worse - for electricians.See above - potentially better for building owners and landlords, and may save the tenant a call out to find/replace a hidden fuse.Rather than either being "much better" I'd say the pros/cons of each option are more or less balanced.0 -
IMHO, 'intended use' is a red herring. It's just a socket - a fused spur with a switch. Hardwiring is needed only in bathrooms (or similar) and for high-power appliances.A WM is pretty easy to pull out and if it blew a fuse then, most likely, it needs checking anyway.0
-
Eldi_Dos said:Ectophile said:Eldi_Dos said:The electrician could solder the multicore cable before putting into screw down terminal.Nobody does that any more. It's worse than not soldering them. Bootlace ferrules are the correct solution if the terminals aren't designed for stranded conductors.But since all appliances have used stranded conductors for decades, I can't think why an outlet wouldn't be designed to take them.
The fitting in the photo looks like it could be decades old.- The solder will wick up the copper wire a few millimetres. Stranded copper wire is quite flexible, and can withstand being bent back and forth a few times. Wire that's full of solder can't flex, and can easily snap when bent.
- Solder isn't at all springy. If crushed, it stays crushed. Copper isn't very springy, but it's better than solder. Over time, the brass contacts that the wire goes into will warm up and cool down. That could be because of the high current being drawn when the machine is heating up, or even because of the change of seasons. As the brass terminals cool down, they contract a little, crushing the solder. As the terminals warm up, the terminal expands, but the solder doesn't spring back, and the screw terminal becomes a little loose. After a few years, the terminals can have worked totally loose, and they can overheat and catch fire.
If it sticks, force it.
If it breaks, well it wasn't working right anyway.1 -
Ectophile said:Eldi_Dos said:Ectophile said:Eldi_Dos said:The electrician could solder the multicore cable before putting into screw down terminal.Nobody does that any more. It's worse than not soldering them. Bootlace ferrules are the correct solution if the terminals aren't designed for stranded conductors.But since all appliances have used stranded conductors for decades, I can't think why an outlet wouldn't be designed to take them.
The fitting in the photo looks like it could be decades old.- The solder will wick up the copper wire a few millimetres. Stranded copper wire is quite flexible, and can withstand being bent back and forth a few times. Wire that's full of solder can't flex, and can easily snap when bent.
Her courage will change the world.
Treasure the moments that you have. Savour them for as long as you can for they will never come back again.0 -
Ectophile said:Eldi_Dos said:Ectophile said:Eldi_Dos said:The electrician could solder the multicore cable before putting into screw down terminal.Nobody does that any more. It's worse than not soldering them. Bootlace ferrules are the correct solution if the terminals aren't designed for stranded conductors.But since all appliances have used stranded conductors for decades, I can't think why an outlet wouldn't be designed to take them.
The fitting in the photo looks like it could be decades old.- The solder will wick up the copper wire a few millimetres. Stranded copper wire is quite flexible, and can withstand being bent back and forth a few times. Wire that's full of solder can't flex, and can easily snap when bent.
- Solder isn't at all springy. If crushed, it stays crushed. Copper isn't very springy, but it's better than solder. Over time, the brass contacts that the wire goes into will warm up and cool down. That could be because of the high current being drawn when the machine is heating up, or even because of the change of seasons. As the brass terminals cool down, they contract a little, crushing the solder. As the terminals warm up, the terminal expands, but the solder doesn't spring back, and the screw terminal becomes a little loose. After a few years, the terminals can have worked totally loose, and they can overheat and catch fire.
Been having a bit of bother with broadband recently, after usual remote tests and checks a engineer came out this morning and on checking the phone socket where external cable entered house found there was verdigris on wires at screw terminals,replaced socket and things seem better now.If the wires had been tinned I am sure the problem would not have arisen and think it is good policy to shape and tin wires with a bit of solder if dealing with screw terminals in legacy equipment. But only time will tell.0 -
This thread has attracted my interest because I replaced my washing machine recently and all I had to do was plug it in. However, it is plugged into an extension type cable in that there is a fused switch above the worktop but seemingly, a cable has been wired into that switch and an unswitched plug socket added to the end of it. So all I had to do was unplug the old machine and plug in the new machine.
it’s not an extension lead in the normal sense but it effectively does the same job as it allows the plug of the washing machine to be positioned out of the way underneath the cupboards, so as not to restrict the available space for the washing machine.
is this not a recommended approach? It’s been like that since the builders built the house 10 years ago (with the builders having wired it that way).Northern Ireland club member No 382 :j0 -
I suspect it is a switched fused spur - Perfectly acceptable way of doing it.All my below counter sockets are wired up that way. It means th appliances can be isolated without dragging them out.Her courage will change the world.
Treasure the moments that you have. Savour them for as long as you can for they will never come back again.0 -
Eldi_Dos said:Ectophile said:Eldi_Dos said:Ectophile said:Eldi_Dos said:The electrician could solder the multicore cable before putting into screw down terminal.Nobody does that any more. It's worse than not soldering them. Bootlace ferrules are the correct solution if the terminals aren't designed for stranded conductors.But since all appliances have used stranded conductors for decades, I can't think why an outlet wouldn't be designed to take them.
The fitting in the photo looks like it could be decades old.- The solder will wick up the copper wire a few millimetres. Stranded copper wire is quite flexible, and can withstand being bent back and forth a few times. Wire that's full of solder can't flex, and can easily snap when bent.
- Solder isn't at all springy. If crushed, it stays crushed. Copper isn't very springy, but it's better than solder. Over time, the brass contacts that the wire goes into will warm up and cool down. That could be because of the high current being drawn when the machine is heating up, or even because of the change of seasons. As the brass terminals cool down, they contract a little, crushing the solder. As the terminals warm up, the terminal expands, but the solder doesn't spring back, and the screw terminal becomes a little loose. After a few years, the terminals can have worked totally loose, and they can overheat and catch fire.
Been having a bit of bother with broadband recently, after usual remote tests and checks a engineer came out this morning and on checking the phone socket where external cable entered house found there was verdigris on wires at screw terminals,replaced socket and things seem better now.If the wires had been tinned I am sure the problem would not have arisen and think it is good policy to shape and tin wires with a bit of solder if dealing with screw terminals in legacy equipment. But only time will tell.Living the dream in the Austrian Alps.0 -
I am not at electrician, but I always solder ends of stranded wires if I can (except, possibly, 4mm2 and thicker) and I have never seen a wire broken because of this. IMHO, it's an urban legend.
0 -
grumbler said: I am not at electrician, but I always solder ends of stranded wires if I can (except, possibly, 4mm2 and thicker) and I have never seen a wire broken because of this. IMHO, it's an urban legend.
Her courage will change the world.
Treasure the moments that you have. Savour them for as long as you can for they will never come back again.2
Confirm your email address to Create Threads and Reply
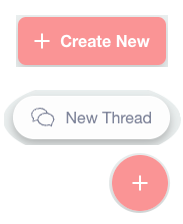
Categories
- All Categories
- 351.2K Banking & Borrowing
- 253.2K Reduce Debt & Boost Income
- 453.7K Spending & Discounts
- 244.2K Work, Benefits & Business
- 599.3K Mortgages, Homes & Bills
- 177K Life & Family
- 257.6K Travel & Transport
- 1.5M Hobbies & Leisure
- 16.2K Discuss & Feedback
- 37.6K Read-Only Boards