We'd like to remind Forumites to please avoid political debate on the Forum... Read More »
📨 Have you signed up to the Forum's new Email Digest yet? Get a selection of trending threads sent straight to your inbox daily, weekly or monthly!
How important are torque settings on bolts?
Options
Comments
-
-
moonrakerz wrote: »I don't quite get the "90 degree" thing............
You torque down to the required figure or until the wrench "breaks" - you DO NOT torque it any further !
okay doke, cyclinder heads for example are torqued because its an easy to use measure to see how tight something is but the fact of the matter it is the ''stretch'' of the bolt that matters, so when they say to torque to x and add 90degrees its to try and counter the resistance and friction (which knocks out the torque setting) in the threads and use the bolt to its full potential.
Its there for a reason, if simon says jump you should jump.0 -
Gloomendoom wrote: »Huh? If the specs say you torque it down and then add 90°, then that is what you do.
If you do that there is absolutely no way of knowing what the thing is actually torqued down to - so there is no point in giving a figure in the first place.0 -
moonrakerz wrote: »If you do that there is absolutely no way of knowing what the thing is actually torqued down to - so there is no point in giving a figure in the first place.
Why would it matter, the spec in the handbook is tried and tested for best performance by the oem.0 -
moonrakerz wrote: »If you do that there is absolutely no way of knowing what the thing is actually torqued down to - so there is no point in giving a figure in the first place.
You don't need to know. The manufacturer has deduced the correct specs for you and the torque figure is just part of the process.
Do you question the validity of the the torque figures they provide too?0 -
Coincidentally I used my torque wrench today (it's the same one as mikey72 linked to) to refit my steering wheel bolt (35Nm). If your doing car work regularly you should get one considering they are very reasonably priced. I don't find I need to use it often because I only use it for important bolts like head bolts, steering wheel nut, timing belt tensioner and idler bolts, etc. I went through a phase of using it for wheel nuts but I just use a breaker bar now.
Haynes lists the torque setting for things like sump plugs and hundreds of other things but I don't bother getting the torque wrench out every time I do an oil change! I just use it for important stuff.
There is the issue that cheaper torque wrenches might not be as accurate as expensive ones but unless your a professional or using your torque wrench all the time then a cheaper one should do fine!0 -
moonrakerz wrote: »If you do that there is absolutely no way of knowing what the thing is actually torqued down to - so there is no point in giving a figure in the first place.
Angles are more accurate, precisely because of the problem highlighted by someone earlier in the thread that of lubrication. A lubricated thread/bolt will go further in add more pressure to the head/more stretch to the bolt for the same amount of applied torque than a dry bolt/thread.
So where angles are used they usually give a low torque starting point which is not so affected by lubrication, and even if it was affected, any effect will be minimised by the low torque starting point so overall the final torques will be closer to what they should be.
Regarding new bolts, some haynes manuals will quote max bolt lengths IIRC, if they are below this you need not use new bolts. You can also pretty safely re-use your bolts at least once. But then again they only cost a few quid to get new ones your call.0 -
It also states that it should be tightened by 90degrees. Do I understand this to mean that you should tighten to the torque parameters and then a finally once more, turn it clockwise 90 degrees from that point?
Yep, the way to do it by eye, what I do, is to put the socket&bar on the bolt, take up the slack, then use something 90 degrees on the bar to show your end position, make a mental note of a place on the car a bolt, a screw head, a VIN plate anything, a chalk mark. Turn the bar until you are on top of that mark/place and stop.0 -
Coincidentally I used my torque wrench today (it's the same one as mikey72 linked to) to refit my steering wheel bolt (35Nm). If your doing car work regularly you should get one considering they are very reasonably priced. I don't find I need to use it often because I only use it for important bolts like head bolts, steering wheel nut, timing belt tensioner and idler bolts, etc. I went through a phase of using it for wheel nuts but I just use a breaker bar now.
Haynes lists the torque setting for things like sump plugs and hundreds of other things but I don't bother getting the torque wrench out every time I do an oil change! I just use it for important stuff.
There is the issue that cheaper torque wrenches might not be as accurate as expensive ones but unless your a professional or using your torque wrench all the time then a cheaper one should do fine!
Sump plug is one of the main things I use it for.
The alloy sump on mine is prone to stripping, or seizing up, if you mess it up.0 -
This discussion has been closed.
Confirm your email address to Create Threads and Reply
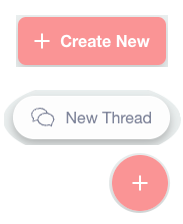
Categories
- All Categories
- 351.2K Banking & Borrowing
- 253.2K Reduce Debt & Boost Income
- 453.7K Spending & Discounts
- 244.2K Work, Benefits & Business
- 599.3K Mortgages, Homes & Bills
- 177K Life & Family
- 257.7K Travel & Transport
- 1.5M Hobbies & Leisure
- 16.2K Discuss & Feedback
- 37.6K Read-Only Boards