We'd like to remind Forumites to please avoid political debate on the Forum... Read More »
📨 Have you signed up to the Forum's new Email Digest yet? Get a selection of trending threads sent straight to your inbox daily, weekly or monthly!
Grade two Listed 15th Century Oak Frame Barn Conversion - Advice On Heating & Flooring
Options
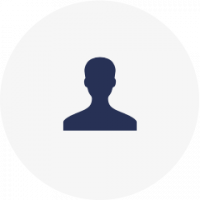
BarnConversionProject
Posts: 1 Newbie
Hello, due to embark on this project later this year. I am due a SAPS survey which will give me the recommended options for heating and insulation thickness but I would like to hear from people who have completed a similar barn conversion and what their choices were and why?
We aim to complete and sell on within a few years and do not have a never ending budget therefore need to ensure wise choices are made.
Barn facts -
15th century barn circa 500 years old - Oak frame to be restored/repaired alongside underpinning before anything else can begin. The internal space will end up extended to 2000 sqft this includes one closed in upper mezzanine level for one bedroom, all other rooms will be downstairs.
I am making enquiries with flooring companies regarding polished concrete flooring for all rooms (apart from the bedrooms) as I am told this is the cheaper option as we have to lay new foundations and floor anyway? I also do like the polished concrete floor for such an open space. If chosen the polished concrete would span utility room, toilet, open plan hall, kitchen, living, dining, hallway, bathroom and ensuite.
Is this the best option for price and durability? What should I expect to pay?
Regarding heating I keep being advised to go for underfloor heating with a heat source pump but I need convincing. Any advice on the best option? We are not connected to mains gas.
Sorry that's a chunk! Advice appreciated.
We aim to complete and sell on within a few years and do not have a never ending budget therefore need to ensure wise choices are made.
Barn facts -
15th century barn circa 500 years old - Oak frame to be restored/repaired alongside underpinning before anything else can begin. The internal space will end up extended to 2000 sqft this includes one closed in upper mezzanine level for one bedroom, all other rooms will be downstairs.
I am making enquiries with flooring companies regarding polished concrete flooring for all rooms (apart from the bedrooms) as I am told this is the cheaper option as we have to lay new foundations and floor anyway? I also do like the polished concrete floor for such an open space. If chosen the polished concrete would span utility room, toilet, open plan hall, kitchen, living, dining, hallway, bathroom and ensuite.
Is this the best option for price and durability? What should I expect to pay?
Regarding heating I keep being advised to go for underfloor heating with a heat source pump but I need convincing. Any advice on the best option? We are not connected to mains gas.
Sorry that's a chunk! Advice appreciated.
0
Comments
-
Have a chat with Mike Wye about foamed glass (for insulation) and limecrete rather than concrete.Limecrete is more sympathetic for old buildings, and you are likely to get a better response from your Conservation Officer when using "traditional" materials... And please, don't go slapping modern cement (and that includes stuff like K-Rend) on the walls.Her courage will change the world.
Treasure the moments that you have. Savour them for as long as you can for they will never come back again.1 -
Make sure that any insulation is breathable - there are so many good resources on the Historic England website, don't let the designers use modern details as they won't be appropriate. I would want an architect who had a lot of experience with historic buildings to be driving this, not a SAP assessor.
And make sure that proper heat loss calculations are done to size the heating system, the heat loads for barn conversions can be much larger than people expect, particularly with the large volumes and normally poor air tightness. At your size you're going to be at the very top end of the single domestic heat pump range, so important to get that right.0 -
Yes indeed. Careful. Get the roof right for what you are trying to do and as energy practical as possible.
UFH is desirable. Wish my converter had done it. As without destroying nice floors and digging down in an already converted one - it's a right pain to retrofit. And it would make my move off kero a lot easier if it was there. You are digging anyway. Now is good.
Barns do often have the room for rads - in a lot of cases. But design ideas may dictate you don't want them
In any event doing a conversion today - you will want low temperature emitters. That's large - yes really large - triple rads like Stelrad K3 or better. Download the data sheets and you will see what the same heat output looks like at a wide conventional DeltaT (kero or gas boiler) and a "most efficient" low temperature ASHP lower DeltaT. You don't do smaller rads and run an ASHP hot. That's a road to ruin.
It is probably much better all else equal as a design to go UFH with care going into the pad, insulation, floor covering design so that it heats the house not the ground. And then an ASHP could work the way it wants to and the design can be radiator free or radiator free downstairs although these can be fiddly to blend with UFH - but people do it a lot. Fiddly not impossible.
Even though higher temperature ASHPs exist (a bit) the technology is generally more cost effective at a lower working temperature. Higher COP = lower bills. I would start there.
You may want 3phase if the supply is being added anyway and it isn't prohibitive to get it on site. House + ASHP + Car Charger + Electric Range cooker etc. 100A can become a constraint requiring picking from a subset of these items. And it allows more grid connected solar if fitting a lot of that features in your plans or it could be an add on in the future proofing of the conversion.
Back to what is happening or not happening to the roof again and what it will be made of
I have lived in an earlier conversion with single phase and faced choices about which electrical things - car charges, electric cookers, ASHP fitted into 100A. And was limited on grid connected solar.
Barn roofs are a key step to get right first time. Open apexes are extremely pretty but a nightmare of thin insulation between exposed not very straight or even beams, Interior plasterboard doesn't stay sealed to beams for long. So the quality of the insulation and any sealing/taping is key. Open apex is not good at holding heat and a huge area of air for it to rise up into.
A pretty roof to look at within - with a better roof behind and above it can address this. With whatever planning need on top. Though this may involve raising the roof - it depends. It's where design meets practicality and cost and whether the roof has to come off in the first place - how much is going back up - what can readily be done from below and what happens between rafters from above.
I have looked at a fair few barns while examining upgrading my old one. And the interiors have sometimes been disappointingly lacking in character even odd and a bit oppressive due to a lack of apertures and planning constraints on these - but often better insulated and boarded up with well insulated interior ceilings. So higher performers on that.
And sometimes visited beautiful but slightly impractical ones - striking in terms of ancient timbers, even exposed brickwork, vast full height windows - but a nightmare on stilts to heat.
Having experienced an older barn getting the kero out once designed in is tough. Ignoring the risibly inefficient kerosene Aga scenario (Just No !!!!). You don't burn any oil for DHW in the summer (to speak of) and a design now would sort that with tank solar input (grid connected solar or direct). You use relatively little in swing season for heating. Especially if you have a site with tree trimming and can have a few stove fires with local stuff. You will have a stove to cope with overhead power cuts lasting more than a day won't you ?
Its the peak cold months where all the oil gets burned. And if you size for peak / worst case weather with an ASHP instead of a large oil boiler to get the kero out that's going to sting financially too. Peak heat load at -15C outside and the defrost cycle will not look attractive. Better insulation competently done is key. But many recommend a smaller ASHP setup with a contingent "booster" arrangement of whatever sort - fossil boiler, woodstove, basic electric heaters, oil filled rads, to boost for the would otherwise be cold - so do the thing - scenario. I wouldn't put oil in as backup. And the hour is late to do it as a primary too. But people still do. Electric things. And a woodstove fallback for when electric is off. Relatively inexpensive item.
The SAPS will illustrate the issues and onging costs for you.
I don't much like pellets (supply, storage, operation, not really energy dense enough). I do like woodstoves - because it is a heat source even a cooker - when the power is off for a couple of days due to storms and a big outage where they triage repairs.
But particulates are an issue. Less so rural. But for you if you are sensitve to them.
Some sites a GSHP will be more practical than ASHP (lots of flattish ground for coils) rather than drilling deep pits but I haven't used one. They are less common AFAIK
Get the glazing right. This is tough if there are large and odd apertures, curved tops etc.
Sectional windows can help reduce crane stuff and permit manual handling. If developing to flog on quickly then cheap windows is what it is. For longer lived windows and lack of maintenance then powder coated metal to the exterior with timber/plastic/metal to interior could be the way to go. Mine had very cheap softwood with meh double glazing which defied me to keep it coated on weather aspects every 18 months. So when it went after a sad 20 years or so - AluClad timber went in. I may never recover from the cost of that though. But a quick wash off and you are done. So no decorator costs.
+1 to the thoughts upthread on breathable structure. It is possible to build a sealed MVHR house within a house and let the "old" structure continue to stand round it - if you are careful. Or it is possible to better insulate an old structure but with breathable materials but it will never be as passive or sealed up. (And in some ways that's a good thing as lack of ventilation brings new and different concerns. It is not a good idea to mix in the wrong materials and play sealed structure games on older walls and roofs not built for residential at all or certainly of an era when ventilation and breathable was intrinsic to design.
The other biggie is getting old meets new, aperture detailing, avoiding cold bridging, window depths vs the insulation, air seals all that stuff not only specified correctly but *actually done like that*. Ditto internal insulation fitted around heritage structure. The joy of the self builder going for 100% neat or the nightmare of the customer of the poorly site supervised builder with typical subbies and a hands off architect. Bodging away merrily and boarding it up.
0 -
I looked into buying a grade II cottage, and the listing was a major issue. The local conservation officer does not want room proportions to change, so adding insulation to the exterior walls is not allowed, for example. Solar panels are completely out of the question. This is an early 20th century building.With a 15th century listed structure, would there be really serious constraints on what you are allowed to do?If building a mezzanine floor, for instance, will that perhaps need to be completely freestanding, within the existing structure, and not joined onto it?Or, maybe, there’s more leeway with a barn than a cottage?would it be better starting from the point of view of what you’re allowed to do, rather than what you would like to do?No reliance should be placed on the above! Absolutely none, do you hear?0
Confirm your email address to Create Threads and Reply
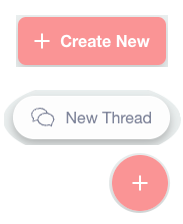
Categories
- All Categories
- 351.1K Banking & Borrowing
- 253.2K Reduce Debt & Boost Income
- 453.7K Spending & Discounts
- 244.1K Work, Benefits & Business
- 599.2K Mortgages, Homes & Bills
- 177K Life & Family
- 257.5K Travel & Transport
- 1.5M Hobbies & Leisure
- 16.1K Discuss & Feedback
- 37.6K Read-Only Boards