We'd like to remind Forumites to please avoid political debate on the Forum... Read More »
We're aware that some users are experiencing technical issues which the team are working to resolve. See the Community Noticeboard for more info. Thank you for your patience.
📨 Have you signed up to the Forum's new Email Digest yet? Get a selection of trending threads sent straight to your inbox daily, weekly or monthly!
What should I ask my windows joiner before installation?
Options
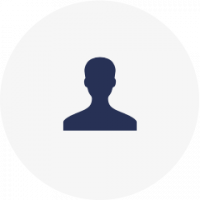
Skag
Posts: 480 Forumite

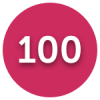
I was wondering, are there any common caveats that I should consider based on your experience from replacing old wooden sash windows with new ones? Or any lessons learned so that I ask them to include them in the schedule of work.
Maybe something that you wished you knew before you replaced yours?
0
Comments
-
We had this done in a very old house, the only issue is that it took twice as long to install as they had expected as there was a lot of work to be done after the old window was out before the new frames could go in. But there's really no way of knowing until they take the old one out.
Make sure you've seen samples of the window furniture before they come to install.
1 -
Check for the presence of a lintel supporting the outer leaf of brickwork. If you have a big lump of stone visible on the outside, no problem. If it is plain brick (or a soldier course), the timber frame is often providing support. Sometimes it is easy to wriggle a steel in, other times, you have to remove a load of bricks above the window - This bumps up the cost quite a bit.
Her courage will change the world.
Treasure the moments that you have. Savour them for as long as you can for they will never come back again.1 -
FreeBear said:Check for the presence of a lintel supporting the outer leaf of brickwork. If you have a big lump of stone visible on the outside, no problem. If it is plain brick (or a soldier course), the timber frame is often providing support. Sometimes it is easy to wriggle a steel in, other times, you have to remove a load of bricks above the window - This bumps up the cost quite a bit.
0 -
Skag said:I was wondering, are there any common caveats that I should consider based on your experience from replacing old wooden sash windows with new ones? Or any lessons learned so that I ask them to include them in the schedule of work.Maybe something that you wished you knew before you replaced yours?1
-
ss2020jd said:Skag said:I was wondering, are there any common caveats that I should consider based on your experience from replacing old wooden sash windows with new ones? Or any lessons learned so that I ask them to include them in the schedule of work.Maybe something that you wished you knew before you replaced yours?
Yes, they are.
1 -
I'm no expert on the rules on lintels per your situation. But be careful.
Installer won't view fitting a not specified lintel and cutting out more brick work to make room for it and then fitting it as "making good".
In my experience you need to be very clear what "making good" means on your interior. Doesn't deal with all possible surprises when you open up. But it sets a baseline for the expected detail and work to interior sills, plaster, window edges. tapes, board and skim, cavity closers, dealing with voids. foaming etc. whatever it is that is likely to be encountered in your openings - especially if the old to new profile changed enough to damage interior reveals significantly.
They'll view knocking bricks about and lintels as a chargeable extra or worse. And will do one of two things. Bodge the install to run off quick (without the lintel) i.e. just whack it in the existing brick aperture in place of the old one. Bill. Run. Cycle company regularly as per standard procedure. Shrug.
Or if they are a bit more professional about regs and they encounter a situation where action does need to be taken - they will take the old window out and then when you are open to weather with them and windows on site have the "Aha you need a lintel guv" extra cost conversation (materials and labour) or it won't meet regs. And your options other than to agree at that point are ?
What they very likely won't do is any great amount of extra masonry work across a number of apertures, fit lintels and eat the cost if fitting lintels doesn't feature in the quote.
So if you know you actually need lintels. Are they on the quoted bill of materials. Is fitting them on the SOW. Is it priced as included or as a contingency item at a known cost per aperture ?
If you think this is a genuine problem it's best to address commercials up front on getting to a compliant version of the solution you want. With a last bit of holdback money tied to completion including issue of certs if they are the self cert FENSA sort.
This is a right old pain but with window retrofit. A really clear understanding of both the installation detail and the activities expected - written down - against the final contract signed against latest version of quote is very helpful to avoid arguments in the thick of it.
After that is all settled and the right size windows turn up undamaged on site - you only need to stand over the probably daily changing crew to make sure they actually do *that* and not some random thing they pulled out of their backside because each individual fitter or joiner "usually does it like this" + nobody looks at the drawing and it is all soon covered up anyway so who is going to know. Gotta love British building.
Good luck.
0 -
Skag, how old is your house, and could you post a photo of the outside, showing the area above the window? Hopefully folk on here can advise on the likely structure, and presence of a lintel.
The windows themselves - have you compared manufacturing methods? My brother had timber sash windows fitted a good few years back now, but I remember some of the research I did came up with things like 'engineered' timber, which is the timber being used for its construction being made up of laminated timbers. This gives a lack of knots, and a far more stable material compared to 'off-the-tree' timber - eg, much reduced chance of a sash warping and becoming sticky in operation.
Also I think there was 'heat-treated' timber, which gave it a natural rot-resistance and even added strength? (Not sure about the last bit.)
The above applied to softwood construction.0
Confirm your email address to Create Threads and Reply
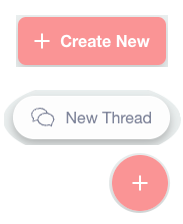
Categories
- All Categories
- 350.8K Banking & Borrowing
- 253.1K Reduce Debt & Boost Income
- 453.5K Spending & Discounts
- 243.8K Work, Benefits & Business
- 598.7K Mortgages, Homes & Bills
- 176.8K Life & Family
- 257.1K Travel & Transport
- 1.5M Hobbies & Leisure
- 16.1K Discuss & Feedback
- 37.6K Read-Only Boards