We'd like to remind Forumites to please avoid political debate on the Forum... Read More »
PLEASE READ BEFORE POSTING: Hello Forumites! In order to help keep the Forum a useful, safe and friendly place for our users, discussions around non-MoneySaving matters are not permitted per the Forum rules. While we understand that mentioning house prices may sometimes be relevant to a user's specific MoneySaving situation, we ask that you please avoid veering into broad, general debates about the market, the economy and politics, as these can unfortunately lead to abusive or hateful behaviour. Threads that are found to have derailed into wider discussions may be removed. Users who repeatedly disregard this may have their Forum account banned. Please also avoid posting personally identifiable information, including links to your own online property listing which may reveal your address. Thank you for your understanding.
📨 Have you signed up to the Forum's new Email Digest yet? Get a selection of trending threads sent straight to your inbox daily, weekly or monthly!
Building Survey findings - Advice please
Options
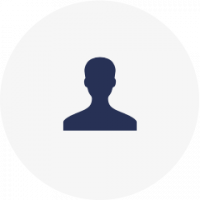
g0009348
Posts: 109 Forumite

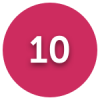
Hello,
I've received my buildings survey results back today, and I'm concerned with the findings for the 1930's semi I want to buy. I've read back over lots of posts on here before starting this thread and understand the services, namely Gas, electric, Water, Heating, Drainage pretty much always come back as a 3 so I'll ignore those, but would welcome advice on the others findings rated as a 3. I'll attempt to summarise
Main Walls - Rating 3
Main walls to the property are of solid construction which is approximately 230 mm thick. Walls to the rear extension are of cavity construction, which is 300mm thick. The main walls to this property are of solid 9 inch without a cavity. Due to external render and external paintwork, I was unable to determine the presence of a DPC to the front and rear elevations. However, no dampness was noted internally and it is likely that an effective DPC exists. To the left elevation the DPC was noted to be of slate at a minimum height of 150mm above ground level. I was also unable to determine the presence of a DPC to the rear extension. However, no dampness was noted internally and it is likely that an effective DPC exists, which is likely to be made of plastic. Due to the limitations of the inspection it is not possible to assess the condition of lintels. There was no apparent movement above most wall openings. There is cracking to the external render above the rear reception room patio doors. The render has moved away from the brickwork beneath and care should be taken incase it falls. Due to the presence of the render, I was unable to determine the condition of the brickwork beneath. It is possible that the brickwork is also cracked. There was no cracking noted to the wall internally. Cracking of this nature can be as a result of thermal movement (expansion and contraction of building materials due to changes in temperature and humidity), especially where water has penetrated the render (see below). However, it can also occur due to lintel failure or where windows and doors have been replaced. A lack of support when the doors were replaced in the past can cause the wall to drop slightly, which causes the wall above to crack. When render is removed the brickwork above the door is likely to show stepped cracking indicative of lintel failure. This cannot be confirmed without further intrusive investigations and the removal of the render. If cracking is found when render is removed, I would recommend crack stitching repairs to the cracks to stabilise and prevent further deterioration. Once this work is complete external render repair will be required. The front and rear elevations are covered with a render coating. Some slight cracking (in addition to the above) was noted to the render. Minor cracks can appear due to normal changes in air temperature and moisture. The cracking to the rear elevation where the rear extension abuts the main wall is due to thermal movement of the lead beneath the render. There are areas where the render coating is hollow when tapped. If water has penetrated the render, frost attack can force the render off. Cracks in external rendering, however small, are best fixed as quickly as possible. Please note, where walls are rendered we cannot comment on the condition of the walls beneath and it is possible that there may be defects present beneath the render coating. Render should terminate 150 mm above ground level to prevent soaking moisture up the wall. It was noted to terminate lower than this in part. I also noted that the render terminates at the edge of the window and door reveals to the main rear elevation. Therefore there are gaps and the brickwork beneath is visible. This can allow moisture to penetrate and can cause damp penetration and condensation internally (see section F3). The render should abut the windows/doors and any gaps sealed. The mortar between the bricks (called the pointing) to the left elevation wall has eroded in various locations. Eroded pointing can allow water to penetrate internally. All pointing should be checked closely and any patch repairs carried out as required. Lime mortar should be used to allow the wall to “breath” and although it takes in water, it also expels water. Cement based mortars trap the moisture within the wall, which can lead to water penetration internally. Some of the bricks to the left elevation were beginning to deteriorate (called spalling). Spalled bricks can contribute to water penetration internally. These bricks will require replacement in the future. Spalling brickwork is a problem for many householders this is due to the effects of weathering and they are not always resistant to frost. The only cure for spalling bricks is to take them out completely and replace them one by one. This should be done carefully by drilling holes around the brick thereby isolating it, and not damaging the surrounding bricks. The property features air bricks. Air bricks are used to ventilate the subfloor void, which holds host to the suspended timber flooring inside the property. These should ideally be kept clear and 150mm away from the ground during construction. This height can be estimated at two or three bricks (see section F4). Some of the air bricks to the rear were noted to be too close to the ground.
Roof Structure - Rating 3
Due to the construction of the roof structure over the rear extension, access to view elements such as ventilation, insulation, air gaps and felt are unavailable. We can not say if the construction has complied with these requirements. There should be felt below the roof tiles, and adequate levels of insulation. Ventilation above sloping ceilings is also required. It is not possible to determine if these provisions are in place. You should ask your legal advisor to confirm that Building Regulations approval was obtained for the extension (see section I3). The main roof structure is supported by rafters and purlins with timber collars, struts and hangars. Timber members are generally in satisfactory condition given the age of the property. The roof members may be spanning above the limitations of today's building regulation but the roof was constructed under different standards of practice at the time of construction. There was evidence of moisture staining to some of the timbers and some high damp readings were found where tested. This is caused by condensation (see below). There is felt to the underside of the tiles. This appears satisfactory with no obvious tears. The felt comprises a variety of types, to include: an older breathable type, a more modern breathable felt and an older non breathable felt. All of the under felt should be a breathable membrane to allow ventilation of the roof space. Condensation was noted to the underside of the felt indicating that ventilation is not adequate. When the roof is next recovered, the felt should be replaced with a breathable variety. In the meantime, additional ventilation is required (see below). The wall between this and the neighbouring dwellings (called the party wall) is adequate with no gaps, therefore preventing fire to pass from one property to another, as it should be. A large amount of boarding has been fitted directly over the ceiling joists. Ceiling joists are designed to hold the weight of the ceiling and not much more. If too much weight is added to the boarding, it can cause ceilings below to crack (see section F2). There is sufficient insulation to only part of the roof space. Loft insulation is required to be 270mm or thicker. There is less insulation beneath the boarded areas and any insulation there will be compressed making it less efficient. This can cause cold spots and the potential for condensation and mould to form on the ceiling below. Insufficient insulation will result in lower internal temperatures and higher heating costs. The loft insulation should be increased where the levels are lower to prevent warm air entering the roof space and the formation of condensation. The roof space does not have sufficient ventilation. There is a non breathable felt to large parts of the roof beneath the tiles and there are no vents provided at the eaves (see section E8). My view of the eaves from inside the roof space was limited. Normal daily activities in the living area of the home (such as taking showers and baths, washing and drying clothes, cooking and boiling kettles) produce warm air containing a large amount of water vapour. If the warm air can’t escape through an open window or air vent, it moves around until it finds a cold surface (which could be in the roof space) where it cools and forms condensation. A lack of ventilation in the roof space can cause mould growth and wood rot. Condensation was noted to the underside of the felt and some high damp readings were taken to the timbers (see above). Additional ventilation at the eaves or the insertion of vent tiles should be provided now. The spotlight fittings above the bathroom should be fitted with a protective housing. Without this, any insulation covering the spotlight fittings is a fire risk. This should be checked and rectified soon. The cold water tank is located in the roof space (see section G3). It is sufficiently supported with a wooden timber frame above the ceiling joists. The chimney breast was noted in the roof space to the front stack (see section F5). I believe that a chimney stack and the associated chimney breasts have been removed for a chimney to the rear elevation (see section E1). There is flexible vent ducting passing through the roof space providing ventilation from the bathroom. Warm air going through a cold roof space will cause condensation on the surface of the flexible pipe, which can drip on the floor of the roof space. Ideally any pipe should be insulated. It should also be noted that the flexible pipe can collapse or get squashed by stored material in the roof space and become ineffective. Rigid pipes are more appropriate and acceptable for longevity. It should be noted that I was unable to determine where the ventilation was discharging to. If it is not discharging externally, moist air entering the roof space can increase the condensation issues previously noted. This should be checked and rectified as necessary.
Floors - Rating 3
The ground floors are a mixture of suspended timber and solid concrete construction. The first floors are of suspended timber construction. Most floors were covered with the vendors floor coverings and no intrusive checks were carried out. Floor coverings included tile, laminate and carpet. We have not carried out an intrusive check. We can not take any responsibly if the floor is substandard in terms of construction and detailing. Checking the full construction of the floor requires intrusive checks which is beyond the scope of this report. Modern floor construction details are shown below for information only. Red ash (sulphate bearing hardcore) was used as an infill below concrete floor slabs in some postwar (1945 to early 1970’s) constructed properties, mainly (however not exclusively) located in and around coal mining areas. When sulphates come into contact with a constituent of cement found in most concrete, and water, it can cause a chemical reaction which can result in heaving/swelling of the concrete floor; this is called ‘sulphate attack’. I saw no evidence to suspect the subject property is being affected by sulphate attack, however, please note we have not checked for red ash, as this requires specialist destructive investigation/testing. If certainty is needed you must arrange for exposure of the floor and testing for red ash. Some types of subsoils can contain sulphates too. We have not tested the subsoils. Solid floor constructed prior to 1960 may include no concrete, no compacted hardcore, and no damp membrane. It is possible that quarry tiles are used on made up ground or a thin layer of concrete has been added years later. Checking the full construction of the floor requires intrusive checks which is beyond the scope of this report. A typical suspended timber floor comprises a series of joists supported by external and internal loadbearing walls and covered with floorboards, to reduce joist sizes there were usually intermediate supports known as sleeper walls. These are small walls in rough stone or brickwork built directly on the ground or on small foundations. To keep the joists dry and free from decay cross ventilation is essential. DPCs, often formed in brittle materials such as slate, are common in a house of this age. With suspended timber the end of the joists are vulnerable to timber decay. Subfloor Ventilation appears to be inadequate. Although there are a number of vents present to the front elevation, the number of vents to the rear and left elevations are inadequate. Some of the vents to the rear elevation are also too low to the ground. The ventilation requires improvement. Please note we have not carried out an intrusive check. If greater assurance is needed then subfloor and the upper floors must be exposed. We have not checked the condition of the sub floor joists for any decay, the condition of the air bricks and their ability to repel water ingress (see section E4). Although no excessive springiness was noted to the timber ground floors, it is recommended that a damp and timber report be instructed to determine if any decay is present to areas that are out of sight. Some of the timber floors creaked underfoot. The most common reason for floors creaking is the use of incorrect nails holding the floor down to the joists. In the case of chipboard floors these nails should be annular ring nails. These nails (usually 2 inches long) have serrations all round the shaft and are slightly screw like in appearance. There may also have been an insufficient quantity of nails used. The floor joists need to be absolutely solid and of the correct size to prevent movement across the span they are bridging. There is a table of joist sizes required for any given span, It is also vital that the joists are fixed very solidly at either end. Joists should be spaced at the correct centres (usually 400mm) and cannot move in their wall sockets or joist hangers. The tail of the hanger should be firmly built into the wall and the joist firmly fixed into the hanger. If the joists are built into the wall this should be done in a way which prevents both rotting and rotating. There is a needs for timber spacers or ‘noggins’ at regular intervals across the floor. This is sometimes done in a ‘Herringbone’ fashion using battens but more often these days is done using solid timber the same size as the joists themselves. Absence of these provisions causes creaking. Please note we have not carried out an intrusive check. If greater assurance is needed then subfloor and the first floor must be exposed. Restraining bars and herringbone strutting can help the joists not to creak or creak less. With the creaking of the upper suspended timber floors an intrusive check must be carried out by a timber specialist.
There are various other 2's which I think can be expected with a house of the age, however I would really welcome any advice on the above and whether it is something which I should for further investigation or consider re-negotiation as it will cost money.
Really appreciate all support
I've received my buildings survey results back today, and I'm concerned with the findings for the 1930's semi I want to buy. I've read back over lots of posts on here before starting this thread and understand the services, namely Gas, electric, Water, Heating, Drainage pretty much always come back as a 3 so I'll ignore those, but would welcome advice on the others findings rated as a 3. I'll attempt to summarise
Main Walls - Rating 3
Main walls to the property are of solid construction which is approximately 230 mm thick. Walls to the rear extension are of cavity construction, which is 300mm thick. The main walls to this property are of solid 9 inch without a cavity. Due to external render and external paintwork, I was unable to determine the presence of a DPC to the front and rear elevations. However, no dampness was noted internally and it is likely that an effective DPC exists. To the left elevation the DPC was noted to be of slate at a minimum height of 150mm above ground level. I was also unable to determine the presence of a DPC to the rear extension. However, no dampness was noted internally and it is likely that an effective DPC exists, which is likely to be made of plastic. Due to the limitations of the inspection it is not possible to assess the condition of lintels. There was no apparent movement above most wall openings. There is cracking to the external render above the rear reception room patio doors. The render has moved away from the brickwork beneath and care should be taken incase it falls. Due to the presence of the render, I was unable to determine the condition of the brickwork beneath. It is possible that the brickwork is also cracked. There was no cracking noted to the wall internally. Cracking of this nature can be as a result of thermal movement (expansion and contraction of building materials due to changes in temperature and humidity), especially where water has penetrated the render (see below). However, it can also occur due to lintel failure or where windows and doors have been replaced. A lack of support when the doors were replaced in the past can cause the wall to drop slightly, which causes the wall above to crack. When render is removed the brickwork above the door is likely to show stepped cracking indicative of lintel failure. This cannot be confirmed without further intrusive investigations and the removal of the render. If cracking is found when render is removed, I would recommend crack stitching repairs to the cracks to stabilise and prevent further deterioration. Once this work is complete external render repair will be required. The front and rear elevations are covered with a render coating. Some slight cracking (in addition to the above) was noted to the render. Minor cracks can appear due to normal changes in air temperature and moisture. The cracking to the rear elevation where the rear extension abuts the main wall is due to thermal movement of the lead beneath the render. There are areas where the render coating is hollow when tapped. If water has penetrated the render, frost attack can force the render off. Cracks in external rendering, however small, are best fixed as quickly as possible. Please note, where walls are rendered we cannot comment on the condition of the walls beneath and it is possible that there may be defects present beneath the render coating. Render should terminate 150 mm above ground level to prevent soaking moisture up the wall. It was noted to terminate lower than this in part. I also noted that the render terminates at the edge of the window and door reveals to the main rear elevation. Therefore there are gaps and the brickwork beneath is visible. This can allow moisture to penetrate and can cause damp penetration and condensation internally (see section F3). The render should abut the windows/doors and any gaps sealed. The mortar between the bricks (called the pointing) to the left elevation wall has eroded in various locations. Eroded pointing can allow water to penetrate internally. All pointing should be checked closely and any patch repairs carried out as required. Lime mortar should be used to allow the wall to “breath” and although it takes in water, it also expels water. Cement based mortars trap the moisture within the wall, which can lead to water penetration internally. Some of the bricks to the left elevation were beginning to deteriorate (called spalling). Spalled bricks can contribute to water penetration internally. These bricks will require replacement in the future. Spalling brickwork is a problem for many householders this is due to the effects of weathering and they are not always resistant to frost. The only cure for spalling bricks is to take them out completely and replace them one by one. This should be done carefully by drilling holes around the brick thereby isolating it, and not damaging the surrounding bricks. The property features air bricks. Air bricks are used to ventilate the subfloor void, which holds host to the suspended timber flooring inside the property. These should ideally be kept clear and 150mm away from the ground during construction. This height can be estimated at two or three bricks (see section F4). Some of the air bricks to the rear were noted to be too close to the ground.
Roof Structure - Rating 3
Due to the construction of the roof structure over the rear extension, access to view elements such as ventilation, insulation, air gaps and felt are unavailable. We can not say if the construction has complied with these requirements. There should be felt below the roof tiles, and adequate levels of insulation. Ventilation above sloping ceilings is also required. It is not possible to determine if these provisions are in place. You should ask your legal advisor to confirm that Building Regulations approval was obtained for the extension (see section I3). The main roof structure is supported by rafters and purlins with timber collars, struts and hangars. Timber members are generally in satisfactory condition given the age of the property. The roof members may be spanning above the limitations of today's building regulation but the roof was constructed under different standards of practice at the time of construction. There was evidence of moisture staining to some of the timbers and some high damp readings were found where tested. This is caused by condensation (see below). There is felt to the underside of the tiles. This appears satisfactory with no obvious tears. The felt comprises a variety of types, to include: an older breathable type, a more modern breathable felt and an older non breathable felt. All of the under felt should be a breathable membrane to allow ventilation of the roof space. Condensation was noted to the underside of the felt indicating that ventilation is not adequate. When the roof is next recovered, the felt should be replaced with a breathable variety. In the meantime, additional ventilation is required (see below). The wall between this and the neighbouring dwellings (called the party wall) is adequate with no gaps, therefore preventing fire to pass from one property to another, as it should be. A large amount of boarding has been fitted directly over the ceiling joists. Ceiling joists are designed to hold the weight of the ceiling and not much more. If too much weight is added to the boarding, it can cause ceilings below to crack (see section F2). There is sufficient insulation to only part of the roof space. Loft insulation is required to be 270mm or thicker. There is less insulation beneath the boarded areas and any insulation there will be compressed making it less efficient. This can cause cold spots and the potential for condensation and mould to form on the ceiling below. Insufficient insulation will result in lower internal temperatures and higher heating costs. The loft insulation should be increased where the levels are lower to prevent warm air entering the roof space and the formation of condensation. The roof space does not have sufficient ventilation. There is a non breathable felt to large parts of the roof beneath the tiles and there are no vents provided at the eaves (see section E8). My view of the eaves from inside the roof space was limited. Normal daily activities in the living area of the home (such as taking showers and baths, washing and drying clothes, cooking and boiling kettles) produce warm air containing a large amount of water vapour. If the warm air can’t escape through an open window or air vent, it moves around until it finds a cold surface (which could be in the roof space) where it cools and forms condensation. A lack of ventilation in the roof space can cause mould growth and wood rot. Condensation was noted to the underside of the felt and some high damp readings were taken to the timbers (see above). Additional ventilation at the eaves or the insertion of vent tiles should be provided now. The spotlight fittings above the bathroom should be fitted with a protective housing. Without this, any insulation covering the spotlight fittings is a fire risk. This should be checked and rectified soon. The cold water tank is located in the roof space (see section G3). It is sufficiently supported with a wooden timber frame above the ceiling joists. The chimney breast was noted in the roof space to the front stack (see section F5). I believe that a chimney stack and the associated chimney breasts have been removed for a chimney to the rear elevation (see section E1). There is flexible vent ducting passing through the roof space providing ventilation from the bathroom. Warm air going through a cold roof space will cause condensation on the surface of the flexible pipe, which can drip on the floor of the roof space. Ideally any pipe should be insulated. It should also be noted that the flexible pipe can collapse or get squashed by stored material in the roof space and become ineffective. Rigid pipes are more appropriate and acceptable for longevity. It should be noted that I was unable to determine where the ventilation was discharging to. If it is not discharging externally, moist air entering the roof space can increase the condensation issues previously noted. This should be checked and rectified as necessary.
Floors - Rating 3
The ground floors are a mixture of suspended timber and solid concrete construction. The first floors are of suspended timber construction. Most floors were covered with the vendors floor coverings and no intrusive checks were carried out. Floor coverings included tile, laminate and carpet. We have not carried out an intrusive check. We can not take any responsibly if the floor is substandard in terms of construction and detailing. Checking the full construction of the floor requires intrusive checks which is beyond the scope of this report. Modern floor construction details are shown below for information only. Red ash (sulphate bearing hardcore) was used as an infill below concrete floor slabs in some postwar (1945 to early 1970’s) constructed properties, mainly (however not exclusively) located in and around coal mining areas. When sulphates come into contact with a constituent of cement found in most concrete, and water, it can cause a chemical reaction which can result in heaving/swelling of the concrete floor; this is called ‘sulphate attack’. I saw no evidence to suspect the subject property is being affected by sulphate attack, however, please note we have not checked for red ash, as this requires specialist destructive investigation/testing. If certainty is needed you must arrange for exposure of the floor and testing for red ash. Some types of subsoils can contain sulphates too. We have not tested the subsoils. Solid floor constructed prior to 1960 may include no concrete, no compacted hardcore, and no damp membrane. It is possible that quarry tiles are used on made up ground or a thin layer of concrete has been added years later. Checking the full construction of the floor requires intrusive checks which is beyond the scope of this report. A typical suspended timber floor comprises a series of joists supported by external and internal loadbearing walls and covered with floorboards, to reduce joist sizes there were usually intermediate supports known as sleeper walls. These are small walls in rough stone or brickwork built directly on the ground or on small foundations. To keep the joists dry and free from decay cross ventilation is essential. DPCs, often formed in brittle materials such as slate, are common in a house of this age. With suspended timber the end of the joists are vulnerable to timber decay. Subfloor Ventilation appears to be inadequate. Although there are a number of vents present to the front elevation, the number of vents to the rear and left elevations are inadequate. Some of the vents to the rear elevation are also too low to the ground. The ventilation requires improvement. Please note we have not carried out an intrusive check. If greater assurance is needed then subfloor and the upper floors must be exposed. We have not checked the condition of the sub floor joists for any decay, the condition of the air bricks and their ability to repel water ingress (see section E4). Although no excessive springiness was noted to the timber ground floors, it is recommended that a damp and timber report be instructed to determine if any decay is present to areas that are out of sight. Some of the timber floors creaked underfoot. The most common reason for floors creaking is the use of incorrect nails holding the floor down to the joists. In the case of chipboard floors these nails should be annular ring nails. These nails (usually 2 inches long) have serrations all round the shaft and are slightly screw like in appearance. There may also have been an insufficient quantity of nails used. The floor joists need to be absolutely solid and of the correct size to prevent movement across the span they are bridging. There is a table of joist sizes required for any given span, It is also vital that the joists are fixed very solidly at either end. Joists should be spaced at the correct centres (usually 400mm) and cannot move in their wall sockets or joist hangers. The tail of the hanger should be firmly built into the wall and the joist firmly fixed into the hanger. If the joists are built into the wall this should be done in a way which prevents both rotting and rotating. There is a needs for timber spacers or ‘noggins’ at regular intervals across the floor. This is sometimes done in a ‘Herringbone’ fashion using battens but more often these days is done using solid timber the same size as the joists themselves. Absence of these provisions causes creaking. Please note we have not carried out an intrusive check. If greater assurance is needed then subfloor and the first floor must be exposed. Restraining bars and herringbone strutting can help the joists not to creak or creak less. With the creaking of the upper suspended timber floors an intrusive check must be carried out by a timber specialist.
There are various other 2's which I think can be expected with a house of the age, however I would really welcome any advice on the above and whether it is something which I should for further investigation or consider re-negotiation as it will cost money.
Really appreciate all support
0
Comments
-
It’s almost 100 years old. Don’t think there is much there to worry about - standard surveyor covering their backside.
put some insulation in the roof and around the pipes. Costs about £100 to do yourself depending on area. ventilate the house (yep, open the windows!). They haven’t looked under the floor so you’ll need to see if you need a few more nails or screws to stop the creaking.30th June 2021 completely debt free…. Downsized, reduced working hours and living the dream.0 -
Thank you. Really appreciate the reply.
I may see if I can get a further opinion on the crack above the patio doors, I think thats my real concern0 -
Hi OP,
No advice but just wanted to say we are going through a similar headache trying to buy a 1930s semi. Render cracking is causing a problem and also because its on clay soil (like most of the South East) it has a high subsidence risk consequently we've been refused standard buildings insurance. I was wondering what did you decide and did you manage to get insurance?0 -
Hello, I havent got as far as the insurance part yet. I've sent extracts over to the estate agent, explaining there are a lot of things on the survey I will ignore like 3's for gas, electric, heating etc because that just seems a precaution. There are however some I am concerned about, which are x.y and z. I havent asked for a value discount off the purchase price, just said these are the costs my surveyor is advising, lets agree on a suitable way forward with this. I'm hoping the seller will make an offer which I find suitable, rather than me just say this price or I walk0
Confirm your email address to Create Threads and Reply
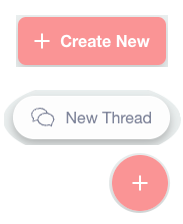
Categories
- All Categories
- 351K Banking & Borrowing
- 253.1K Reduce Debt & Boost Income
- 453.6K Spending & Discounts
- 244K Work, Benefits & Business
- 599K Mortgages, Homes & Bills
- 177K Life & Family
- 257.4K Travel & Transport
- 1.5M Hobbies & Leisure
- 16.1K Discuss & Feedback
- 37.6K Read-Only Boards