We'd like to remind Forumites to please avoid political debate on the Forum... Read More »
We're aware that some users are experiencing technical issues which the team are working to resolve. See the Community Noticeboard for more info. Thank you for your patience.
📨 Have you signed up to the Forum's new Email Digest yet? Get a selection of trending threads sent straight to your inbox daily, weekly or monthly!
Garden Room Build - Cladding and Ventilation
Options
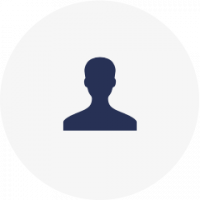
efunc
Posts: 415 Forumite

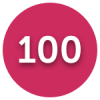
Anyone here built one of these, or something similar? I'm halfway through a small Garden Room which is a lean-to structure against the corner of my garden. This is how it stands now and I'll be fitting vertical T&G larchwood cladding:




I was starting to think about ventilation and just realised I've probably got the wrong end of the stick so need to get back to basics and re-learn what I need to do here. There are 3 main structural cavities in the building:
1 - The one between the outer timber cladding and the exterior OSB face. (I'm just using 19mm battens, not counter-battens, before fitting vertical T&G larchwood cladding)
2 - The one between the interior OSB face and the PIR insulation. About 15 - 20mm in my case
3 - The room itself
The only ventilation I was considering was just the interior of the room (3) with trickle vents on the doors and one 229x154mm 'passive' hit and miss vent. I'm now wondering if this is really necessary at all.
In fact Cavity 3 (the actual room) doesn't really need additional ventilation I believe - it's more for the benefit of the inhabitants rather than the building itself, so trickle vents are sufficient and in the summer the doors can just be opened up. Is that right?
Cavity 2 functions in tandem with the insulation and should be air sealed, so no need to ventilate this.
It's Cavity 1 that I've probably got wrong. This should have been counter battened to enable unimpeded airflow from bottom to top. I'm just fitting horizontal battens however, onto which my vertical cladding will be secured. Ergo, no airflow. To try to improve this I propose cutting out several 2 inch gaps into the horizontal battens, just less than the width of a cladding strip, and also secure stainless steel rodent mesh at the bottom batten gap and at top one too. At the rear of the structure I won't fit cladding right up the rear back wall of the lean-to. Instead I'll leave a 1 inch gaps here and block it off with another strip of mesh. I'll also install a louvre vent in the cladding in each of the two side walls to vent cavity 1. None of this is quite as effective as counter-battens, but is it likely to be effective enough? Any better tricks I can employ instead? I don't want to do counter battens at this stage because of the additional wall thickness and the door/window sills are already going to be too short.
Thanks for any advice.




I was starting to think about ventilation and just realised I've probably got the wrong end of the stick so need to get back to basics and re-learn what I need to do here. There are 3 main structural cavities in the building:
1 - The one between the outer timber cladding and the exterior OSB face. (I'm just using 19mm battens, not counter-battens, before fitting vertical T&G larchwood cladding)
2 - The one between the interior OSB face and the PIR insulation. About 15 - 20mm in my case
3 - The room itself
The only ventilation I was considering was just the interior of the room (3) with trickle vents on the doors and one 229x154mm 'passive' hit and miss vent. I'm now wondering if this is really necessary at all.
In fact Cavity 3 (the actual room) doesn't really need additional ventilation I believe - it's more for the benefit of the inhabitants rather than the building itself, so trickle vents are sufficient and in the summer the doors can just be opened up. Is that right?
Cavity 2 functions in tandem with the insulation and should be air sealed, so no need to ventilate this.
It's Cavity 1 that I've probably got wrong. This should have been counter battened to enable unimpeded airflow from bottom to top. I'm just fitting horizontal battens however, onto which my vertical cladding will be secured. Ergo, no airflow. To try to improve this I propose cutting out several 2 inch gaps into the horizontal battens, just less than the width of a cladding strip, and also secure stainless steel rodent mesh at the bottom batten gap and at top one too. At the rear of the structure I won't fit cladding right up the rear back wall of the lean-to. Instead I'll leave a 1 inch gaps here and block it off with another strip of mesh. I'll also install a louvre vent in the cladding in each of the two side walls to vent cavity 1. None of this is quite as effective as counter-battens, but is it likely to be effective enough? Any better tricks I can employ instead? I don't want to do counter battens at this stage because of the additional wall thickness and the door/window sills are already going to be too short.
Thanks for any advice.
0
Comments
-
OK, so no thoughts on ventilating the space between sheathing and cladding, however my thoughts are turning back to the inside space again.
So... is it sufficient to reply on only trickle vents for the sole ventilation, or is that potentially dangerous? The room is 2.1m x 3.1m and 2.1m high, so about 15.5m3 in volume. It is well insulated all the way round with 100mm PIR and fully vapour sealed on the inside. None of the windows can open, only the doors, consequently the only ventilation possible, apart from opening the doors, is the two trickle vents. So the room is very small, pretty sealed, and will be used in mild weather with no boiling kettles, showers, moisture generating activities taking place, just a desk and chair. However I'm concerned about having oxygen to breath should anyone fall asleep or something for a few hours and only the trickle vents are open.
I did look at "Approved Document F Ventilation" on The Planning Portal yesterday and it seemed to only be concerned about kitchens, bathrooms, utility rooms, etc. Places where a lot of humidity might lurk. The only figures I could find was for the smallest space (<50m3) recommending a vent size of 35000mm2, so there doesn't seem to be that much requirement for ventilation. My trickle vents are 2 x 30cm long so that alone seems to cover things.
Installing an additional little louvre (sliding hit and miss) vent, about 127x75mm is a possibility, but I don't want to have to cut into the wall unless it's dangerous just to rely on the 2 trickle vents. Anyone any ideas?0 -
I can't see your pictures, but have you built it specifically to be airtight, with the exception of the trickle vents? Because most buildings aren't and it will have other, unintended means of ventilation anyway.Everything that is supposed to be in heaven is already here on earth.
0 -
Yes, it's a small summerhouse, but built according to modern construction techniques, so fully insulted slab, DPM, insulated walls, roof, and interior vapour control layer sealing it off before plasterboard. The exterior is going to be clad to breath and vent moisture out. Doors/windows are double glazed and should be pretty draft proof.0 -
Looks good!
I'd suck it and see, but I reckon you won't die with those trickle vents.
If you start to encounter it feeling humid while we've still got some warmer weather left, then consider something extra...
It's finding the balance. No point putting all the insulation in and knocking a hole in the sideEverything that is supposed to be in heaven is already here on earth.
0 -
Well, the problem is that the best time to put a vent in the wall is now, before I put up the plasterboard, do the plastering and outside cladding. Unfortunately I don't have any firm knowledge or figures relating to ventilation so it's all guesswork. I could go ahead and finish it, but then would have to put a lot more effort in afterwards if I found out more ventilation would be required.
The trickle vents amount to about 6000mm2 of vent space, which doesn't amount to much, but may be just enough for a room volume of 15.5m3. I could really do with some tables to confirm though.0 -
Bit late now, but you could have had an opening window0
-
Bit late now, but you could have had an opening window
Possibly not too late, but I agree - a small opening window would have been a good solution. Extra ventilation when you need it. I have one in my garden office which is from Green Retreats and very similar in design and construction to OP's.
It's only 3x3m and has French doors and glazing at the front and a small window at just above desk height and it's perfect for through ventilation in the Summer (no matter how well insulated it is, I find the solar gain from the front glazing still means it gets uncomfortably hot in the height of Summer).
It's possibly not too late to reframe a section of one wall and fit a small (approx. 400x800mm) window, it would just require proper detailing around the frame to maintain the continuity of the vapour barrier inside and breather membrane outside.0 -
My advice would be to ask this on the The Woodhaven Forum, on the “workshop builds” section. Lots of people there building their own sheds/workshops who could help.0
-
Thank you for all the useful replies. It's not quite too late to put in a window, but it would be pretty disruptive at this stage and cause some delays. It honestly never occurred to me whilst a slaved over the design for almost a year. Maybe once, but I dismissed it as low priority, and now I regret that slightly.
However I want to just unpick the different reasons for having a window that can be opened. One is for moisture control. Another is for heat control and cooling in the summer, and another if for allowing in fresh oxygen for habitation.
The trickle vents will go some way towards managing the small amount of moisture caused by someone sitting at a desk with a laptop and a cup of tea I presume.
Regarding uncomfortably high temperatures; I don't think this will be a problem with my build. It's very shaded being in the corner of a garden against a boundary wall with trees and houses alongside it giving it shade and shelter most of the day. The front is East facing and really doesn't get much direct sun. In the high heat of summer I would imagine opening the doors would resolve any overheating, however I agree that at night and in evenings when opening the doors out would be undesirable you'd be pretty stuck.
That just leaves my main concern; that of having enough air to breath if you were to be closed in for hours and maybe having a doze. In this case would I be advised to have one additional wall vent (127x75mm) just to be safe?
We screeded the floor now and put most of the insulation up today. Need to just seal gaps and then do a VCL before plasterboarding:
Starting to feel cozy..0 -
FWIW mine is NE facing and it still gets very hot in Summer. Opening the doors helps of course, but I feel like having the window is also helpful and sometimes I don’t want the doors wide open.
I’ve never had any problem with condensation though, I would imagine your trickle vents will be sufficient.0
This discussion has been closed.
Confirm your email address to Create Threads and Reply
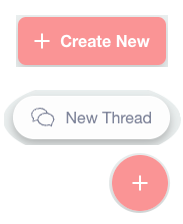
Categories
- All Categories
- 350.8K Banking & Borrowing
- 253K Reduce Debt & Boost Income
- 453.5K Spending & Discounts
- 243.8K Work, Benefits & Business
- 598.6K Mortgages, Homes & Bills
- 176.8K Life & Family
- 257K Travel & Transport
- 1.5M Hobbies & Leisure
- 16.1K Discuss & Feedback
- 37.6K Read-Only Boards