We'd like to remind Forumites to please avoid political debate on the Forum... Read More »
📨 Have you signed up to the Forum's new Email Digest yet? Get a selection of trending threads sent straight to your inbox daily, weekly or monthly!
Changing coil spring
I have removed the front suspension strut - 2003 Punto
I have compressed the spring
I now have to find a 27mm ring spanner for the piston nut (allen key needed to hold the piston still) if I don't have one I'll use an adjustable spanner or a mole grip or water pump pliers.
The book says on re building this piston nut has a torque of 60 lbft
says to use a crows foot, I have some big crows feet and hopefully one will fit.
But my question is if I measure the the nut in the fitted position the distance from the nut to the top of the strut -say 25mm- and then on refitting I just tighten the nut to the same position, that would be just as good as torquing it surely.
My next question is that the top strut nut in the engine bay also has a torque value and will also require a crows foot.....but because of the cup a crows foot would not fit inside the cup. I don't have a 19mm crows foot......because of the cup it would have to be a deep crows foot if there is such a thing. .......It's a pity they can't design the piston so that you can lock it into position by having a hole through it for example so you hold it in place with screwdriver through the hole whilst someone else torques the 2 nuts.
For the top nut (44 lbft) I will have to replicate by hand/memory what I know to be the approximate pressure required to turn a nut already torqued to 44 lbft.
Or I could use a deep 19mm socket and cut a large hole out of the side of it and pass the allen key through the hole.
My other thought is an engineering question:
I wonder how accurate a crows foot torque is compared with a directly applied torque? Do you think they take into consideration that it will be applied with a crows foot when they set the torque value?
So for example if a direct torque is 100 Lbft
How much would a crows foot torque have to be applied to reach the same direct torque? Would it be more or less? It would surely be less because of the extra distance and Bending Moment principle. But I can't work out if there is an error developed by the way the turning moment is being applied to the side rather than from above
I have compressed the spring
I now have to find a 27mm ring spanner for the piston nut (allen key needed to hold the piston still) if I don't have one I'll use an adjustable spanner or a mole grip or water pump pliers.
The book says on re building this piston nut has a torque of 60 lbft
says to use a crows foot, I have some big crows feet and hopefully one will fit.
But my question is if I measure the the nut in the fitted position the distance from the nut to the top of the strut -say 25mm- and then on refitting I just tighten the nut to the same position, that would be just as good as torquing it surely.
My next question is that the top strut nut in the engine bay also has a torque value and will also require a crows foot.....but because of the cup a crows foot would not fit inside the cup. I don't have a 19mm crows foot......because of the cup it would have to be a deep crows foot if there is such a thing. .......It's a pity they can't design the piston so that you can lock it into position by having a hole through it for example so you hold it in place with screwdriver through the hole whilst someone else torques the 2 nuts.
For the top nut (44 lbft) I will have to replicate by hand/memory what I know to be the approximate pressure required to turn a nut already torqued to 44 lbft.
Or I could use a deep 19mm socket and cut a large hole out of the side of it and pass the allen key through the hole.
My other thought is an engineering question:
I wonder how accurate a crows foot torque is compared with a directly applied torque? Do you think they take into consideration that it will be applied with a crows foot when they set the torque value?
So for example if a direct torque is 100 Lbft
How much would a crows foot torque have to be applied to reach the same direct torque? Would it be more or less? It would surely be less because of the extra distance and Bending Moment principle. But I can't work out if there is an error developed by the way the turning moment is being applied to the side rather than from above
0
Comments
-
I wouldn't worry about the torque values.
Yes a good guide to measure the thread left or compare to other side if visable.
Just make sure they are tight.0 -
I've done tons f shocks over the years and to be honest, I've never worried about torque values.
The only time I would is on something important on the engine such as tensioners etc. Truth is though that torque wrenches can be a bit of a pain. I bought one from a leading retailer and it over torqued some bolts and stripped the thread in the engine block. Result? £150 to have helicoils fitted.
I spoke to a mechanic at Haynes a few years back about ford ka shocks and why the nut on topwas a bit troublesome and kept stripping the thread where the allen key goes. He said although they officially provide values he always does things by hand to where it 'feels right'. Can't say much better than that really!0 -
Agreed, common sense is still the best tool you can find, and it can't be bought.0
-
I don't think aero engine service technicians would agree.
Certain bits on a car do have importance, requiring a TW.
On other bits though experience can be enough, but that experience had better be right. I have often had to finish a job on experience and this will probably be one of those occasions.
But I believe in doing things right and if money or just ingenuity can solve the problem then it becomes a balance of....
whats right Vs practicality Vs importance0 -
-
Do it by feel and not excessively tight or the next person to do the job will be using the gas hammer. Tightening to the old mark is irrelevant as the joint has been disturbed so it wont be in the exact, same, original condition, so the torque value will be different (hysteresis).0
-
Do it by feel and not excessively tight or the next person to do the job will be using the gas hammer. Tightening to the old mark is irrelevant as the joint has been disturbed so it wont be in the exact, same, original condition, so the torque value will be different (hysteresis).
I was talking about the spring compression nut, not the strut top nut...
The new spring would be the almost the same as the old one was when new, and so tightening to the old position will be almost exactly the same surely?0 -
I was talking about the spring compression nut, not the strut top nut...
The new spring would be the almost the same as the old one was when new, and so tightening to the old position will be almost exactly the same surely?
there is a infintismal amount of movement to the nut with wear.
I just mark them up with a marker before removal, and tighten up to the mark.
wouldn't worry about torque values.
unless you putting on a subframe a cylinderhead or tensioners and cam pullys and camshafts and cranks.0 -
The position of the nut has nothing to do with the torque to get it there. In such a simple application it might be close, but you haven't taken the strut apart for fun, so there will be different loads in the whole sub assembly.0
-
Ok, I was misunderstanding the construction of the strut assembly....never having dismantled one of these before....I thought that nut actually compressed the coil spring..... it doesn't, I can see that now.
I have now dismantled it and removed the coil spring (that was fun without a the proper spanner that fitted it!). The nut in question actually tightens down a bearing onto a 'shoulder' on the piston. So measuring the thread distance is a waste of time, because it will still tighten down onto the 'piston shoulder' at that point.
Now I will buy a new coil spring ...there was some confusion 2 motor factors told me a single price for a single part then a 3rd motor factor said "it depends if the car has got A/C or not there are 2 diferent coils"...??? So I thought I'd take it off before paying for the new one. I can't see how A/C would change the coil spring.
Anyways on reassembly I am going to buy a 27mm crows foot (about £11) and use the torque wrench. Either that or I buy a 27mm ring spanner and tighten it by approximation.
Can anyone help to determine the crow foot torque to get an actual torque of 60 lbft? depends how big the crow foot is but is there a formula?0
This discussion has been closed.
Confirm your email address to Create Threads and Reply
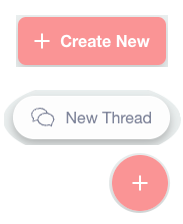
Categories
- All Categories
- 351.4K Banking & Borrowing
- 253.3K Reduce Debt & Boost Income
- 453.8K Spending & Discounts
- 244.4K Work, Benefits & Business
- 599.7K Mortgages, Homes & Bills
- 177.2K Life & Family
- 258K Travel & Transport
- 1.5M Hobbies & Leisure
- 16.2K Discuss & Feedback
- 37.6K Read-Only Boards