We'd like to remind Forumites to please avoid political debate on the Forum... Read More »
📨 Have you signed up to the Forum's new Email Digest yet? Get a selection of trending threads sent straight to your inbox daily, weekly or monthly!
How to tie into/seal to existing 1928 damp proof course
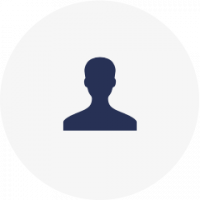
Fevvahz
Posts: 30 Forumite
I've recently bought a 1928 built 3 bed semi. The floors were uneven, so they've had to be dug up, and were about to build up using modern standards. The old floor consisted of parquet wood blocks on top of cement and rumble, to a depth of about 5 inches. The damp proof course used when first built appears to be slate layers, which I understand was common practice.
We've dug to 15" in order to provide a good base, and fit in the required insulation etc. We've checked with local building control who've specified what they want to see and when. However I'm wondering if there's a way to tie the damp proof sheeting layer into the existing wall, or seal it against the wall to stop damp coming up the wall, around the edge of the slab and rotting the flooring/skirting board?
Ive read on other threads/forums we will be creating, a high pressure moisture area is created around the edge of the slab. Is there perhaps a product which could be applied to the wall/DPC which would bond it nicely together? We were thinking perhaps a bitumen type affair?
Thanks in advance.
We've dug to 15" in order to provide a good base, and fit in the required insulation etc. We've checked with local building control who've specified what they want to see and when. However I'm wondering if there's a way to tie the damp proof sheeting layer into the existing wall, or seal it against the wall to stop damp coming up the wall, around the edge of the slab and rotting the flooring/skirting board?
Ive read on other threads/forums we will be creating, a high pressure moisture area is created around the edge of the slab. Is there perhaps a product which could be applied to the wall/DPC which would bond it nicely together? We were thinking perhaps a bitumen type affair?
Thanks in advance.
I have a blog too...
0
Comments
-
Hi Fevvahz,
You are quite right to be concerned about dampness emerging at the solid floor / wall joint whether that be a new or existing solid floor and this is often a cause of low level dampness to plaster and timbers in contact with that joint such as skirting, base of door frames / architraves / base of stairs etc. Often this is misdiagnosed as failure of the damp proof course (dpc).
With a new floor this will tend to settle over time and the floor will also move seperately to the walls surrounding it. When a modern house is being built it is easy to seal the floor damp proof membrane (dpm) or vapour barrier into the wall dpc but as you describe with an existing older property it is not possible without opening walls up to truly overlay and seal such a dpm into the wall dpc. Accordingly what you are wanting to achieve is a flexible impervious barrier at the floor / wall joint that seals from the dpm into a raked out area of the dpc that will accomodate floor / wall differential movement.
Bitumen as you suggest is impervious but not very flexible and may crack over time. I have seen the detail undertaken with silicone sealants that will accomodate such movement. I have also seen the floor / wall joint sealed with products such as Wykamol Technoseal DPM, or Safeguard Vandex BB75 with BB75E additive incorporating scrim within the coats, or Vandex Unimortar 1, (contact addresses given below) well worked into all voids, cracks etc in min two coat work though in my opinion these are less flexible than the silicones. Also remember that plaster should not bridge the dpc and be kept at least 25mm from the floor / wall joint. Be mindful that as indicated above you need the sealing of the floor / wall joint dpc / dpm to extend to areas such as base of door frames / architraves, skirting and base of stairs etc so these will need opening up to gain access.
Contact addresses for manufacturers of above products:
Safeguard Chemicals - Redkiln Close , Redkiln Way, Horsham, Sussex, RH13 5QL (contact Mr Brian England (tel 01403 210204 or 07801661615) www.safeguardeurope.com
Wykamol Group – Unit 3, Boran Court, Network 65 Business Park, Hapton, Burnley, Lancashire BB11 5TH (contact Mr Andrew Latimer tel 0845 4006666)
www.wykamol.com
Sovereign Chemicals – Park Road, Barrow-In-Furness, Cumbria. LA14 4QU ( tel 01229 870800 )
www.sovereignchemicals.com
Hope this helps, kindest regards David Aldred Independent damp and timber surveyor.0 -
Thanks for that reply David - I shall have a look into those products!I have a blog too...0
-
Hi Fevvahz,
I suspect that this problem may cost more money than necessery if you go down the route of having to 'seal' the dpm/dpc joint. The main thing is to make sure that the DPM under the floor is well lapped at joints and extends up the wall, above the DPC level. It can then be trimmed off around the perimetier of the floor after the concrete is set.
David is quite right that care is needed, so maybe a temporary timber lath could be fitted to hold the DPM against the wall while the concrete is laid. Thus, any damp at the edges is stopped by the existing DPC, which has not been bridged by the concrete because of the effective DPM.
Acually, there is no 'high pressure' at the floor wall junction. I'm afraid that this is a myth, which I think is from a misunderstanding of how moisture rises through materials. There is only pressure when you are below ground. This is known as hydrostatic pressure and the products David mentioned, particulaly the Vandex materials, are designed to combat this - hence they are high specification and quite costly. Only use them when you really need them.
A more cost effective floor/wall joinst sealer; if you're determined to use one, is Safeguards's Drybase vapour membrane. Which is a liqued pre-mixed solution you can simply brush arround the perimiter of the floor/wall junction. It is not a wearing surface but as it will be under the skirting and door frame sections it will be fine.
Safeguard's contact details are in David's post.
Bryan Hindle CSRT CSSW0 -
One of the concerns is that even with as suggested by others above, tagging the damp proof membrane (dpm) to the surrounding brickwork with a batten, is that because the mortar joints are not a flush joint and the masonry be that brickwork, blockwork or stone is uneven combined with the inevitable wrinkles present when folding and laying the dpm from horizontal to vertical including at corners etc there is a gap between the dpm and the masonry of the wall.
Even with the best will in the world damp vapours can and will emerge up between the dpm and the wall and as I previously indicated because the floor is not tied into the surrounding walls then one will move seperately to the other over time compounding the gap problem. Remember you only need the smallest of gaps between the dpm and the wall that a knife blade can be inserted down to cause damp, degradation and decay to the plaster, timbers and finishes directly sat upon such a gap and in my experience it remains one of the biggest causes of misdiagnosis of dpc failure where solid floors are present.
Now consider a steaming pan of water and putting a lid close to but not completely on top of that pan and it should be obvious that the emerging steam is concentrated at the perimeter gap between the pan lid and the pan itself to a greater degree in this specific area than with no lid at all.
In the same way it may be appreciated that laying an effective dpm over a floor inevitably concentrates moisture attempting to emerge from that floor area at the perimeter of that effective dpm. This can result in increased dampness to perimeter walls themselves above dpc level if there are any weaknesses to the dpc and as discussed an increase in dampness emerging at the floor / wall joint where not effectively sealed. What is really needed is an impervious material that is guaranteed by the manufacturer to accomodate inevitable structural movement between the new floor and the surrounding perimeter walls and when I spoke with Safeguard and Wykamol the products mentioned in my previous post were the only ones they recommended to meet such a requirement.
I have seen other materials used including silicone sealants with great success but please be mindful that using an inferior product that will not provide a flexible impervious seal to the floor / wall joint from the dpm sealing into the dpc (which may be above the level of the floor) on the grounds of cost may not seem like such a good lidea if it results in all the second fix joinery such as skirting etc decaying along with that expensive wallpaper curling and detaching at the base of the wall in a couple of years.
On the coast where we live moisture can and does not only emerge up from the ground by capillarity (rising damp) but also under hydrostatic pressure where in the case of the latter many properties are low lying and ground water tables are unfortunately high. This can be a problem for some types of remedial damp proof courses which are of a type that do not block the pores within the masonry such that this moisture under hydrostatic pressure has been proven to push right up through the chemical dpc even where injected in accordance with the manufacturer's instructions by good contractors. Kindest regards, David Aldred Independent damp and timber surveyor0
This discussion has been closed.
Confirm your email address to Create Threads and Reply
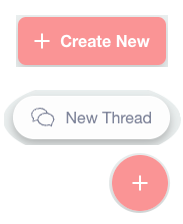
Categories
- All Categories
- 351.3K Banking & Borrowing
- 253.2K Reduce Debt & Boost Income
- 453.8K Spending & Discounts
- 244.3K Work, Benefits & Business
- 599.5K Mortgages, Homes & Bills
- 177.1K Life & Family
- 257.8K Travel & Transport
- 1.5M Hobbies & Leisure
- 16.2K Discuss & Feedback
- 37.6K Read-Only Boards