We'd like to remind Forumites to please avoid political debate on the Forum... Read More »
We're aware that some users are experiencing technical issues which the team are working to resolve. See the Community Noticeboard for more info. Thank you for your patience.
📨 Have you signed up to the Forum's new Email Digest yet? Get a selection of trending threads sent straight to your inbox daily, weekly or monthly!
damp advice please
Options
Comments
-
Hi David
the property is approx 100year old mid terrace with a solid floor. i'm not sure if its cavity or solid wall. Have not had any cavity insulation myself. chimney breast is not on outside wall, its open and has a gas fire in place. there is no mould present. external walls are plain brick not rendered. look forward to hearing your thoughts, kind regards BungrefurbMFiT-T2 Questee number 1460 -
Hi bungrefurb,
Plain brick wall mid terrace built circa 1910 should have been built with a damp proof course to comply with Building Regulations applicable at that time though as yet this is unconfirmed in this particular case.
Check whether the external walls are solid or cavity as this has a significant bearing upon any recommendations. If plain brick externally look for courses at regular intervals up the height of the wall to see if there are any where you can only see half bricks instead of full length bricks and measure the wall across an external doorway / window. Solid walls of minimal thickness tend to be about 9" in depth plus plaster and cavity walls around 11" plus plaster. Report back on your findings.
Chimney breasts are great when used for their original design function of having a roaring coal fire within them in constant use which kept the hearth, fire-back, chimney breast itself all relatively dry. Check to see whether or not the original chimney pots are still open (i.e. no cowlings fitted) although the amount of rainwater that drip down an open flue all the way to ground floor level is often exagerated and this moisture source if a significant problem would tend to be seen at first floor room level chimney breasts before it becomes apparent at ground floor level. Since you haven't mentioned a big problem of first floor dampness to the chimney breast area we can then move onto issues to ground floor chimney breast areas.
Whilst the brickwork forming the sides / rear of the fireplace may have been built with a damp proof course within it (though this is not confirmed) the hearth itself may well not have a barrier to ground moisture beneath it since it woudl be thought the coal fire would keep this area nice and dry. When no longer used for this purpose the hearth may become damp with ground moisture and consequently all that loose infilll material behind the fire-bricks / fire-back too and this can be quite a hefty moisture resevoir especially to a party wall chimney stack where the situation may be mirrored on the other side of the party wall.
The icing on the cake is the soot from the original coal fires will be high in sulphates amongst other contaminates and as the moisture from the hearth as described evaporates outwards it brings with it these contaminates. The moisture then evaporates from the surface but the contaminates are left behind and these accumulate in the plaster of time. This can have the effect of degrading the plaster and also if any of these salts are hygroscopic by their nature they will attract moisture to them from the air within the room (in the same way leaving salt out in a kitchen becomes damp) making the plaster even more damp.
This issue of salts being present is another reason why the problem may be more visible at some times more than others as the relative humidity within rooms fluctuates to correlate with the changing weather.
Ordinary Portland cement often incorporated into base coats of replacement plasters is particularly susceptable to sulphate attack and hence the recommendation to use anti-sulphate cements in such cases.
A domestic gas fire makes nothing like the same amount of heat as the original coal fire would. With both coal and gas fires the fumes can sometimes condense within the flues before exiting the chimney pots.
If the fireplace is not to be used for coal fires any more then under the written guidance and approval of a Gas Safe registered plumber taking the fire-back out along with the damp infill material behind it, removing the damp hearth and casting a new concrete hearth on a damp proof membrane sealed into the surrounding damp proof course in the walls to give one complete barrier to ground moisture is obviously a good start.
The Gas Safe registered plumber to advise / fit suitable cowlings in respect of appliances below to chimney pots where none are fitted.
Degraded plaster / plaster considered at risk of such failure should be removed to well beyond the last sign of the problem and often doing this to the full height of the room is the preferred option. The choice of whether to replace the paster to a grade that is both waterproof and able to hold back disruptive contaminates as described above within the chimney breast will suffice.
However such plastering requires a very high standard of workmanship both with regard to substrate preperation and application of the plaster and unfortunately this is not always forthcoming. The plasterer will want paying whilst the area is still damp and if it fails to dry down / degrades at a later date the plasterer may tend to blame anyone but themselves. In addition there may be a nagging doubt if high readings will be obtained with damp meters by surveyors if the client comes to sell the house at some point in the future if salts have leached into the replacement plaster.
Because of the above there may be a preferance to either have the chimney as feature brickwork or waterproof grade dry lined over its full height which should in the case of the latter have a design function to be a physical barrier to the effects disruptive salts / any dampness issues emanating from the other chimney breast on the other side of the party wall if a party wall stack is applicable.
Regarding chemical damp proof courses to chimney breast areas it should be obvious from the above that attempting establish an effective chemical dpc by injecting blindly into the chimney stack from one side of what could be a joint party wall chimney stack is highly unlikely to be effective given the depth of hearth / masonry and all that loose infill material behind the fire-backs. Accordingly the dpc contractor should if they have any sense exclude this area from their dpc guarantee in a majority of cases and rely upon other methods to address problems in this area.
Specific cases may well vary and accordingly the above are given as general comments only and should not be acted upon. Kindest regards David Aldred Independent damp and timber surveyor
0 -
Hi David
Assuming i have measured correctly 8.5-9 inch depth, and looking at the external wall I can see half bricks at regular intervals. I hope that will help you shed some light on the problem, kind regards bungrefurbMFiT-T2 Questee number 1460 -
Hi Bungrefurb,
From your last post the indications are of one brick thick solid wall construction with solid floors and as previously indicated the age of the property is such that it was likely built with a damp proof course (dpc) under Building Regulations applicable at time of construction but this is not confirmed.
A chemical dpc has been installed recently with associated re-plastering usually up to around 1m high.
Having not actually seen the problem we must cover a number of points to raise possible causes which may or may not apply to this particular case so apologises for covering a number of bases with this unseen case.
The one brick thick external solid wall is of minimal depth and as such is prone to penetrating dampness. The amount of penetrating dampness depends upon a number of things not least of which is pressure difference / exposure. The design function of the wall was for it to suffer wind driven rain but then vent this moisture outwards during more favourable weather. This process can be restricted by re-pointing in a hard dense cement mortar instead of the breathable mortar the house was built with or by say painting such walls externally.
If the pores of the wall become filled with water instead of air the wall will be colder and if it is colder it is more prone to condensation actually occurring not only on internal plaster but also within the depth of the wall itself. Condensation within the wall adds to the penetrating dampness and this can be cumulative such that a moisture resevoir within the wall is formed that may well sustain the unwanted dampness even during more favourable weather such that the situation changes form being transient to constant.
Where such moisture is restricted from evaporating outwards the sun falling upon the wall can actually drive this moisture inwards rather than as might be expected venting it outwards. All of the issues described above excluding other external defects will tend to be most acute at the base of the wall.
The stone cills if present tend to be built through to the rear of the plaster, or at least there is often no physical barrier to dampness between the rear of the cill and the plaster. It is therefore essential the cills are kept water-tight and a drip molding is present on their underside as the stone is often of a type that is porous so issues of penetrating dampness / condensation can be acute here.
The mortar the property was built with can be significant because if of a black ash type then this is derived from coal slag high in sulphates that as described in the previous are disruptive to Ordinary Portland cement if this has been used in replacement plaster from the previous chemical dpc.
The solid floor to the property may or may not be original. Sometimes rear rooms were solid flags / tiles and front rooms suspended timber. The location of the original dpc should have been under the level of the suspended timber floor joists in order to offer them some protection. If you look on the outside of the properties along the terrace then vents to the base of solid walls often are indicative of previous suspended timber floors. If concrete floors replace original timber floors then the original dpc will may well be significantly below the current finsished floor level.
If concrete floors are now in place they may or may not have replaced the types of floors described above which originally would have been likely far more breathable than concrete. Putting such relatively impervious solid floors down will cause an increase in the level of moisture trying to emerge from any gaps between the solid floor and the wall and any weaknesses in the original dpc if it has cracked with settlement of the property.
In older properties of this type there is usually no sealing of any damp proof memebrane in the floor into any dpc in the walls and as the floor moves seperately to the walls over time a gap develops between the wall and the floor where this dampness as described above will readily emerge from, directly into any timber and plaster sat upon this open floor / wall joint. Such timber not only includes skirting but base of door frames / architrave / base of stairs etc and will also include areas unable to be readily seen such as behind fitted units if such gaps are present.
Just to make things even more interesting the level of the original dpc may not be at the finished floor level or indeed below this level if suspended timber floors were there previously but actually one brick or more above the finished floor level, especially where there may have been concrete skirting fitted at some point so the level of the original dpc really does need to be found by sample opening up.
To a mid terraced property on a sloping site one terrace ground floor may be well above or below the level of the subject property and if next doors house is above your house then moisture will tend to push through the party wall for the height difference applicable if not held back by appropriate structural waterproofing. This is not the same thing at all as moisture rising up by capillarity (rising dampness) and the dpc will not hold back such moisture nor is it ever intended to.
The solid floor iself should be checked for dampness often by way of a humidity tent or other means over a 72 hour period.
Add to the above a situation where open coal fireplaces are no longer used and sealing up these hearths plus replacing all the breathable windows and doors with sealed uPVC units lacking trickle vents and you can see how things can begin to go awry. Add to that external issues such as:
Paths laid over each other so they encroach upon the level of the original dpc and possibly bury it. With solid walls the height of 150mm between dpc and paths becomes important because debris blowing against house walls will act to bridge the dpc and rain bouncing off paths will do the same.
Paths sloping down to the property instead of away from directing rainwater from paths to house walls.
Garden walls built into house walls such that they act as a wick feeding dampness into the house walls.
Defective gutters / pointing / sealants etc.
Then add occupancy induced condensation issues, poor heating regimes where the house is allowed to go cold for significant periods and poor insulation.
Since the electrical damp meters do not confirm rising dampness at all but only indicate timber at risk of decay and areas that should be further investigated then perhaps in view of the above you will appreciate the scope for misdiagnosis or simply bad contractors selling dpc's for profit where they are not proven to be required when there is in the majority of cases nothing wrong with the poor old original dpc which may well be generally intact. Be mindful that slate or bitumen dpc's may crack with settlement over time but these natural materials do not disappear and the amount of dampness that would emerge up through such cracks may well not correlate with the full wall lengths of dampness or works recommended by somebody selling yet another dpc.
You may well take the view to insert another dpc but this is your choice and not apparently due to proven dpc failure to date. Try and investigate and address issues described above and note if th eplaster is contaminated it will not recover. Sealing of the floor / wall joint with flexible impervious material is a good start.
Issues regarding re-plastering / waterproof grade dry lining with appropriate vapour barriers go back to that discussed within chimney breast post above but to external walls such dry lining can include insulation being mindful to vent on the cold side of the system externally where applicable to prevent condensation within the system.
The above is not an exhaustive discussion by any means but may get you scratching your head beyond simply paying out for yet another dpc as this will make three in total. It should be obvious that inserting another dpc will not resolve the issues described above if present and if dampness returns the dpc contractor will simply state the problem is nothing to do with them. So before you spend your money just have a think and make sure you are trying to resolve all the moisture sources / issues and not just any rising dampness coming up through the two dpc's already present. As stated before these are general comments only and are not to be acted upon given specific cases may well vary. Kindest regards David Aldred Indpendent damp and timber surveyor
0 -
Hi David
THanks for really indepth info regarding my problem. I forgot to mention the damp patches appear worse when we have heavy rain, is that significant in any way? Also the house does have a problem with condensation. Kind regards bungrefurbMFiT-T2 Questee number 1460
This discussion has been closed.
Confirm your email address to Create Threads and Reply
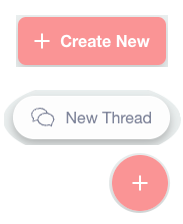
Categories
- All Categories
- 350.9K Banking & Borrowing
- 253.1K Reduce Debt & Boost Income
- 453.5K Spending & Discounts
- 243.9K Work, Benefits & Business
- 598.8K Mortgages, Homes & Bills
- 176.9K Life & Family
- 257.2K Travel & Transport
- 1.5M Hobbies & Leisure
- 16.1K Discuss & Feedback
- 37.6K Read-Only Boards