We'd like to remind Forumites to please avoid political debate on the Forum... Read More »
We're aware that some users are experiencing technical issues which the team are working to resolve. See the Community Noticeboard for more info. Thank you for your patience.
📨 Have you signed up to the Forum's new Email Digest yet? Get a selection of trending threads sent straight to your inbox daily, weekly or monthly!
Chimney damp and the cold weather
Options
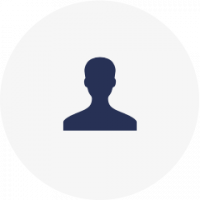
mikebailey00
Posts: 3 Newbie
We recently moved house and have had a problem with damp on our bedroom wall where there is an old, dis-used chimney breast on the outside. The top of the chimney has been removed and the roof tiles go over it. It looked like water had got into the chimney breast but when we got a builder to look at it he said it all looked dry. Anyway, he put a piece of lead over the top so that any further water coming in through the roof would hit the lead and run out over the outside edge of the chimney breast.
That seemed to have solved the problem as the damp patch seemed to be drying out despite all the recent wet weather.
However, over the last day or so it feels like it has got damp again. Im wondering if this could just be due to the cold weather - the moisture in already damp wall being drawn out and condensing on the bedroom side of the wall, where the air is much warmer?
If so then presumably, as the wall continues to dry out the problem will rectify itself.
Does this sound plausible, or is it more likely that water is again entering?
Any help or advice would be much appreciated
Thanks!
Mike
That seemed to have solved the problem as the damp patch seemed to be drying out despite all the recent wet weather.
However, over the last day or so it feels like it has got damp again. Im wondering if this could just be due to the cold weather - the moisture in already damp wall being drawn out and condensing on the bedroom side of the wall, where the air is much warmer?
If so then presumably, as the wall continues to dry out the problem will rectify itself.
Does this sound plausible, or is it more likely that water is again entering?
Any help or advice would be much appreciated
Thanks!
Mike
0
Comments
-
Does the chimney breast have a proper vent fitted in the bedroom (and the room below if relevant)? Old disused chimneys must be ventilated and not sealed up. This will allow air to circulate and any moisture to evaporate.No free lunch, and no free laptop0
-
Yes, there is a vent in the bedroom (in built-in wardobe) but the part that appears to have suddenly got damper is just to the side of this, outside of the wardrobe.
There is a vent downstairs where the old fireplace was also.
Any thoughts?!!!
Thanks0 -
Are the vents open?-they often get closed.
I suspect that with the rain and high winds we've been having recently, some water has got in, I would monitor it and see what develops.No free lunch, and no free laptop0 -
Hi,
Please look at my other posts on this forum regarding chimney breasts and damp / plaster problems and I think you should find the relevant answers you are looking for. If not please let me know and I will write a detailed response on this thread. Kindest regards, David Aldred Independent damp and timber surveyor0 -
Ive had a look round the site and found lots of related issues but not sure what is really applicable here (i.e. the breast has been taken of at the top and covered with roof, etc)
If you are able to let me have some further detail that would be great. We're keen to get this sorted asap but dont know whether its best just to wait and see, or get someone round.
By the way, inside there is wallpaper covering the walls - would it be an idea to take this off in that area so we can see the state of the walls better etc?
Thanks
Mike0 -
Hi Mike,
It sounds like the roof desn't fully cover the stack but that your builder has dressed the area that remains with lead to prevent any moisture ingress down the masonry so all should be well but a few high level photos and photos from inside the loft void would be helpful otherwise we are speculating here.
I have posted a couple of photos on photobucket:
http://s768.photobucket.com/albums/xx324/DavidAldred/
This shows typical chimney breasts that have plaster contaminated with the soot that has migrated from the brick lined flues into the plaster. This may have happended whilst there were original moisture ingress issues that have now been resolved. It happens when the soot inside the flues gets wet and the moisture evaporates into the rooms leaving behind sulphates and other contaminates in the plaster. Once this has occurred you can play around as much as you like with doing things externally but it won't make any difference to the fact that the plaster is contaminated and will not recover. The visual signs tend to come and go with the changes in the weather / relative humidity but do not go away.
The discussion that follows are general comments only and not to be acted upon given that specific cases may well vary
Obviously you need to ensure the area of stack that remains is externally weathertight. Re-pointing the mortar beds should be in a breathable mortar sympathetic to original mortar - i.e. if lime use lime to re-point. If you have dark grey / black mortar this could be black ash mortar made from coal slag which will just compound the problem. Do not use hard dense sand and cement mortars or renders on old properties as they will reduce evaporation outwards from the mortar beds, the mortar behind and bricks will get wetter and the dampness will migrate internally rather than attempt to vent outwards. The bricks will also be more prone to freeze / thaw damage and as the bricks are wetter they are colder and more prone to condensation within them. The thermal conductivity increases and before you know it you have a moisture resevoir on your hands. If the stack is external such that three sides to it are on the outside this is going to act to take heat out from the room and the area will be cold / prone to condensation without a coal fire within it 24 / 7.
Chimney breasts are great for when they are being used for what they are designed for that is having a coal fire within them 24 / 7 which keeps everything usually nice and dry. When they become redundant / gas fires are put in they can become problematic from top to bottom and there are a lot of issues to consider when the redundant chimney stack remains in place but yours has been removed above roof level so at least that is something. (If you want discussion about chimney stacks above roof level and hearths then please ask).
If you are getting a patch of dampness on the ceiling next to the chimney breast too, then check around the chimney breast up in the attic and what you are looking for is timber hard upgainst the chimney breast that is possibly wet / decaying and feeding dampness onto the ceiling and also debris wedges between the chimney breast and surrounding timber. Such debris will often be hygroscopic and attract moisture to it from the air and then feed it into the ceiling below again contaminating the plaster.
If the chimney breast is on an external wall then vent the redundant flues externally and not from the room because if you vent from the room you are letting warm moist air into a cold external fue where it will condense out.
Things to consider:
Somebody competant to go up externally in the area of the stack and photo / video things at that level - photos speak a thousand words and there may still be work to do to make sure the area is weathertight. Even the smallest hole leaks over time so don't take other peoples word for things you need to see it.
Consider Closing off the internal flue vent and putting two in externally - one high, one low level for each and every flue so there is good cross ventilation ensuring they are of a type and position that will not allow wind driven rain to enter.
Go up in attic and ensure all timber is 50mm away from chimney breast and all debris is removed including industial vacuuming away then insulate.
Remove all damp degraded plaster to full room height including covings and sideways at least 400mm beyond the last sign of problem - if dry lining (see below) remove full wall area to that within which chimney breast is located.
Okay so this is where the fun really starts because there are now a couple of options if not more to consider. Re-plaster to an appropriate specification or waterproof grade dry line preferably insulated. Most people opt for re-plastering but this has quite a few hassles:
Re-plastering contaminated brickwork requires a very high standard of workmanship for surface preperation and application of plaster in order to ensure the plaster is not only waterproof but that it holds back salts within the wall. The number of cases I see where the plasterer simply has not done as they were told is considerable. They want paying whilst the wall is still damp, the layperson client has no idea if they have worked to specification or not and if the wall fails to dry down or degrades at a later date they blame anyone but themselves which is rubbish because there are grades of plaster out there that will hold back almost anything if done correctly.
If a client chooses to opt for re-plastering the plasterer needs to rake out all the motar joints 15mm min, treat the substrates with anti-sulphates, if they are using cements in their specification this needs to be anti-sulphate cements with appropriate additives and tanking mortars to ensure all salts are held back and the plaster is waterproof grade. They should never ever put on base coats in the same day as they put on finishing coats as one contracts as it dries and the other expands. Never ever use bonding plasters to these problem areas they will make an area look worse than before you started as they pull anything and everything to them including salts and dampness.
Also the ceiling where degraded needs to be addressed usually by removong 300mm beyond the damp degraded area and replace with foil backed plasterboard ensuring there is a flexible impervious barrier between the chimney breast and the ceiling otherwise the ceiling plasterbaord will pull moisture from the stack to it. Never ever decorate before it is dried down and remember the rate of drying at best is only ever going to be at about 25mm of wall thickness per calender month so a an eighteen inch thick stack is a year and half to dry down! A water based emulsion can be applied as soon as it visibly looking dry but this will be sacrificial and will fail as the wall continues to dry down.
In addition to all of the hassles above with simply re-plastering the chimney breast wall is still going to be damn cold and prone to condensation so consider other options to re-plastering / trusting to god that the plasterer does as they are told / not just what they feel like and consider insulated waterproof grade dry lining systems instead.
With these waterproof grade dry lining systems a layperson can see a physical barrier to salts and moisture being applied to the wall so they have much more confidence straight away. They can be re-decorated far sooner i.e. as soon as the minimal thickness skim coat of plaster finish is dry and any surveyor in the future cannot get a damp meter on the chimney breast brickwork without opening it up so they cannot flag a problem of dampness up. The area is warmer and therefore condensation on the decorative surface is reduced and everybody is happy.
As with anything there are down-sides. The linings systems are thicker than original plasters and this may require adjustment especially around any openings in addition and of most concern those fitting the system need to be so so careful with regard to vapour barriers to ensure they are fully effective and not compromised in any way. This is because if warm moist air is allowed to enter the system it will condense out and trickle down the membrane then come out onto the floor - ooops not good and it will damage anything it comes into contact with. You can help minimise this by not puncturing the system, using adhesive to fasten skirting etc and venting externally on the cold side of the system but that vapour control has to be satisfactory or you can get trouble.
The studded polyethylene membranes go under various trade names such as Oldroyd, Platon, Delta and the insulated plasterboard such as Kingspan Kooltherm or similar. The following manufacturers will usually supply the membranes direct and one of their area reps will if requested often be pleased to come to site and show people how to apply the material. There will still be a need to re-plasterboard the ceiling in areas degraded as discussed above and also a requirement that no timber including timber wedges / grounds etc are left within the wall where they could decay which applies to whether a client chooses re-plastering or dry lining.
Do not use standard grade drywall adhesive to fix the plasterboard to the membrane as it is hygroscopic though there are types which are suitable for damp environments. None of this work needs to be done by a specialist in damp-proofing but Property Care Association member contractors usually have experience in doing this type of thing thogh they may charge 'specialist rates' compared to a good traditional builder who can also usually apply the membrane system or even clients themselves if they feel capable and under the wing / guidance of a manufacturer's representative.
Membrane and specialist plastering / additive suppliers:
Safeguard Chemicals - Redkiln Close, Redkiln Way, Horsham, Sussex, RH13 5QL (tel 01403 210204 ) www.safeguardeurope.com
Wykamol Group – Unit 3, Boran Court, Network 65 Business Park, Hapton, Burnley, Lancashire BB11 5TH (tel 0845 4006666)
www.wykamol.com
Sovereign Chemicals – Park Road, Barrow-In-Furness, Cumbria. LA14 4QU (tel 01229 870800 )
www.sovereignchemicals.com
Hope this goes some way to throwing some light upon the matter. Please remember specific cases may well vary and these are only general comments of principle for discussion only and not to be acted uponKindest regards David Aldred Independent damp and timber surveyor
0 -
Good post DavidYou may click thanks if you found my advice useful0
This discussion has been closed.
Confirm your email address to Create Threads and Reply
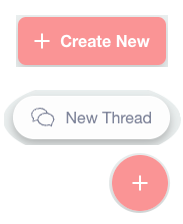
Categories
- All Categories
- 350.9K Banking & Borrowing
- 253.1K Reduce Debt & Boost Income
- 453.5K Spending & Discounts
- 243.9K Work, Benefits & Business
- 598.8K Mortgages, Homes & Bills
- 176.9K Life & Family
- 257.2K Travel & Transport
- 1.5M Hobbies & Leisure
- 16.1K Discuss & Feedback
- 37.6K Read-Only Boards