We'd like to remind Forumites to please avoid political debate on the Forum... Read More »
📨 Have you signed up to the Forum's new Email Digest yet? Get a selection of trending threads sent straight to your inbox daily, weekly or monthly!
Cavity Insulation - Truth of moisture bridging the cavity?
Options
Comments
-
moonrakerz wrote: »I do not wish to sound harsh, but I could pronounce myself to be an expert witness
It's not a matter of opinion it's a phrase with a specific meaning.0 -
replacing wall ties because ???
are your walls moving at all ?
cavity wall insulation works , i had it in my last house and it took the cold out of the hallway and bathroom , i never had damp because of it .
as for damp coming in throught the cavity well the 2 walls dont actually touch each other only by ways of wall ties , which incidently have a "drip" in the middle of them to stop moisture travelling through to inner cavity , also they should be built with the inner wall level or that touch higher then the outside wall to help water run away from inner wall , if built with ties running back towards the inner level then it could cause problems but very minimal .
we actually build houses ... council/social housing as well with full fill cavity batts , meaning if the cavity width is 100mm then we use 100mm width cavity batts so yes completly bridging the cavity ,
somebody previously said the cavitys for an air flow , wrong its an air barrier !! same as double glazeing in principal .
all new houses have some form of insulation in the cavity , and up untill recently a very big housebuilder i work for used mark insulations to inject the cavitys with white insulation stuff .
in my experiance it does work , it does keep your house warmer and to be honest if your getting damp through a cavity wall then their must be a good reason other than cavity wall insulation , it might help assist it but it wouldnt be the main cause of it0 -
Replacing wall ties because they are going bang and causing cracking.0
-
moonrakerz wrote: »I do not wish to sound harsh, but I could pronounce myself to be an expert witness "in matters of dampness and timber problems", and state that I have "proved cavity wall insulation to be the cause" of NO cases of dampness.
I am afraid you have picked a poor phrase; "expert" witnesses have in many recent Court cases have proved themselves to be far from expert.
The Sally Clark case; jailed for murdering her two sons on the "evidence" of an expert witness, who couldn't even master basic maths. Released after 3 years when the expert was totally discredited. She died 4 years later, in her 40s, her mental and physical health destroyed.
They are not experts in far too many cases - just self important people who can force their personal opinions onto others.
Your photos prove nothing whatsoever - the first one looks like a photograph of the planet Jupiter !
"A wet joist" - a duff DPC ? Leaking window frame ? a house in Workington ? oh no ! definitely CWI :rotfl:
Replace wall ties - that's a corker ! Good one for ex double glazing salesmen to have a go at !
My definition of EXPERT !
EX is something that has been !
"s"PERT is a drip under pressure !
shammy0 -
There is no reasons you should not get it installed. Most of the issues people talk about are stories from the fiction section of the library.
o- Years ago (20+) one insulation type was a foam which used to not allow moisture to pass. Believe some would also break down over time as well.
o- Some installers have been known to use the wrong insulation type to save money. Again very rare as there are other easier ways to cut costs.
o- There are multiple times when cavity wall insulation has been blamed but the real problem existing before hand.
Again, don't think about it, just get it installed.0 -
Replacing wall ties because they are going bang and causing cracking.
would they be the old butterfly type wall ties then , just curious as have heard they go rusty and obviously seperate from both walls but wonderd how you find out as their not somthing you can see without knocking a hole in the wall , is this an insurance job ??0 -
Nope, not an insurance job. It was commented on when buying the house that they need to be done and the three people we have had in for quotes have all confirmed that they should be done within the year.0
-
are you having the hole house done or just one wall ?0
-
punknzippy wrote: »would they be the old butterfly type wall ties then , just curious as have heard they go rusty and obviously seperate from both walls but wonderd how you find out as their not somthing you can see without knocking a hole in the wall , is this an insurance job ??0
-
Hi Suisidevw
The following comments are posted in two sections due to the limited number of characters that can be posted within each reply post. I did post comments previously within this thread regarding cavity wall ties / cavity wall insulation along with some photographs on a temporary basis which I have now removed. If anyone wishes to see examples of cavity wall tie problems and cavity wall insulation problems then they should contact me privately by e-mail. However in the meantime the following may be of interest which is not given to preach or convert and I am certainly not prepared to enter into personal arguments regarding the subject matter discussed herein.
The problems to ferrous cavity wall ties within UK housing and commercial properties is discussed within Building Research Establishment (BRE) Digests 329 and 401. The primary cause for concern being structural degradation of the subject building leading to cracking, moisture ingress, decay, structural movement and eventual collapse the latter of which may be sudden, dramatic and without warning.
A wall that is only half a brick thick and say 20 feet long and 18 feet high or considerably higher in some cases is structurally unstable and would fall over in high winds so the function of the cavity wall tie is to give the cavity wall as a whole its required structural integrity whilst at the same time incorporating where such type of tie is used a design feature to prevent moisture tracking across the tie from the outer leaf of brickwork to the inner leaf of masonry where it would tend to cause dampness and other problems if such were to occur.
Original cavity wall ties were made from various materials including brick, slate, stone, copper and of most concern ferrous material. The historic ferrous type of ties which form the bulk of those present in the UK housing stock, before the introduction of superior types of tie, were often given a protective coating of galvanizing or bitumen.
The type and style of these ferrous cavity wall ties present within UK housing stock varies considerably. Some of the simplest are a wire the gauge of a coat hanger bent into a ’Z’ shape and without any drip design being incorporated at all. These wire ties come in various gauges (thicknesses) and more modern ferrous ties were built into a shape similar to a butterfly with twisted ends forming a body and drip design at mid point across the cavity. Other types are plate and cast steel of various designs and gauges. Most ferrous ties are built into the mortar beds horizontally or vertically at set intervals to give the property the structural stability.
The number and pattern of ties present to older housing stock often falls short of modern Building Regulation recommendations which have been revised over the years to reflect experience of what should be adequate with a satisfactory safety margin. However given the box type construction and short expanse of masonry to many types of these older properties where there is a shortfall in the number of ties they often remain stable even with this shortfall in number of ties if the ties themselves remain in good order. It should be obvious that a sheltered small bungalow with hipped roof is less likely to have its outer leaf of brickwork fall off than a three storey gable end to a long terrace with lots of windows in it situated on a hill next to the sea.
As the property is built the bricklayer sometimes accidently allows mortar to fall down the cavity which then sits upon any cavity wall tie it falls upon below. Over time with alterations and exposure further accumulation of debris within the cavity occurs. Air blowing around the cavity picks up this fine abrasive debris and further erodes the wall from inside and all of these issues can compromise the ties making any drip molding to their design (if present) ineffective and consequentially the risk of penetrating dampness across the tie from outside to inside the property increases, along with the risk of any condensation forming upon the tie and similarly tracking inwards.
There is a requirement with many types of cavity wall design that the cavity wall tie should be built into the wall angled slightly upwards in order to resist moisture movement across the tie into the property. This requirement is often failed to be achieved in many housing stock and some ties including more modern and remedial ties often slope inappropriately downwards into the property promoting moisture movement inwards.
The original protective coating such as galvanizing (if originally incorporated) depletes over time especially where it has been initially compromised by the bricklayer bending or knocking the tie with their trowel when they build the tie into the wall during initial construction. The natural mean rate of depletion of the galvanizing for instance is in the order of 15g/m² per year for where the tie is buried in the outer leaf and 7 g/m² where it is buried within the inner leaf. Once the protective coating is compromised the mean rate of corrosion to the mild steel is in the order of 75µm/year per surface or 150µm/year per flat tie. The tie is assumed to have reached the end of its life when one third of its cross sectional area remains. Things obviously vary an awful lot for many reasons but the BRE state the mean nominal life of a vertical twist ferrous tie of say 20x3mm cross sectional area in the outer leaf of masonry is only 13.3 years and for a butterfly tie only 8.9 years in the outer leaf of masonry. The nominal life to the section of tie within the inner leaf is roughly double the life to outer leaf.
The amount of protective galvanizing to ties was reduced around 30 / 40 years ago in a misguided assumption that less would suffice and this led to a glut of prematurely failing ties to properties built at that time. The protective coating was then increased as a result and hence ‘green’ coloured galvanizing came into vogue on the tie to distinguish the increased protection.
The corrosion of the wall ties was accelerated by the use of black ash mortars to many properties which used coal slag high in sulphates that when wet became acidic.
Corrosion of ties is usually worst in the outer leaf of masonry and at higher more exposed levels.
As the tie corrodes it expands to several times its original volume. Mortar is very strong in compression but in comparison very weak in tension such that it cannot cope with the expansion of the tie within it and localised cracking and opening up of the mortar bed occurs where the gauge or size of the tie is significant. This cracking through expansion is unrecoverable and if one is any doubt about this effect photographs can be provided upon request. Over the height of a wall the cumulative effect of each and every tie of large gauge / plate type cracking and opening up the mortar bed will buckle the wall, make it structurally unstable and lift the roof wall plate and the roof itself given the appropriate forces involved. The Egyptians used a similar effect with dry wooden wedges driven into stone that when wetted the wood expands cracking open boulders to the size required.
Resultant failure of the wall is usually sudden and dramatic often during periods of high winds when fluctuating pressures on either side of the outer leaf of masonry ‘pump’ the wall to the point of failure and collapse. Many properties have suffered such a problem and often but not always this is where the exposure rating is severe and the expanse of masonry considerable such as a large gable and / or where there are a lot of penetrations such as windows which weaken the structure.
The BRE Digests give recommendations for remedial action to be taken upon inspecting cavity wall ties. The current recommendation for small gauge wire ties is that the instability caused by their corrosion is minimal such that they may be left within the wall to corrode with additional new ties being inserted to current Building Regulation standards. For larger size / gauge original ties the recommendation is that they should be removed form the wall or isolated by the use of special sleeves to prevent them from causing further damage once new ties as described above have been inserted. This work to address where applicable existing ties to prevent them causing further structural damage is highly disruptive. It requires the opening up of the cavity wall wherever such a tie is present and this means if done externally brick / render removal and all necessary making good or if done internally plaster / brick removal and all necessary making good including re-decoration.
Because it cannot be stated when a wall is about to fail and indeed it would be unsafe for ties to be left to reach that stage, the recommendations of the BRE are measured to reflect the degree of corrosion seen but in short for ties that are noted to be significantly corroded such that red rust is seen upon the ties then remedial action as described above should be undertaken and for ties less seriously corroded then a program of monitoring until such time as remedial works are justified should be initiated.
Given the above and the liability of surveyors mindful of the case law that has already set precedents it is a brave surveyor who would fail to flag a wall tie inspection be undertaken to a property of any significant age. This is especially so when the costs of remedial works are so considerable and the hazard of injury / death to persons and damage to anything below an area of such a collapse is so significant. This is especially true for ties that have to be removed / isolated from the walls and the need for scaffolding or some other safe working platform needs to be provided for cavity wall tie work especially since the new working at height regulations came into force.
It is recommended that the new cavity wall ties inserted be checked by somebody who is not the contractor putting them in and also that this person also check that the contractor has successfully dealt with existing cavity wall ties where necessary. The reason for recommending the former is that the new ties may not be fully effective in tying the wall together just because they are fitted and they should be sample pull tested to ensure they are indeed effective. The guarantee for the work is often just a product guarantee and may not actually guarantee that the wall will remain structurally stable. It is not unknown for contractors to have tied a wall only for it to continue moving outwards until failure occurred and this is often a combination of poor installation, wrong choice of tie type and a type of substrate that was unable to provide sufficient anchor to the new ties such that the tie / substrate interface fails or the tie pulls out a section or core of substrate with it (for example with a resin fix tie) as the wall continues to move outwards at which stage re-building the wall has to be undertaken before inevitable collapse occurs.
Those inspecting should be independent to rule out contractors falsifying successful pull out tests of their own ties and to check sample new ties are also sloping the correct way and not inappropriately encouraging moisture to run down the tie and into the property. The equipment and technique used to test replacement ties is easy to 'hoodwink' any untrained observer into thinking a pull test the contractor is showing them is successful when in truth it may well be anything but.
For example the first pull out test of a sample tie should pull the tie with it anchored to one leaf only (it does not matter whether it is the outer leaf of masory or the inner leaf of masonry just so long as it is able to be confirmed that it is only fixed to one leaf of the cavity wall) and then the following test when the same sample tie has then been fixed to the second leaf of the cavity wall. This is because if you pull from both leaves initially you might actually only be seeing how effective the tie is to one leaf of the cavity wall with no idea whether it is adequately anchored to the other leaf. Also I have seen contractors rig the test equipment so it is pulling on the stop of the meter itself thereby raising the dial on the meter as it is wound up without the equipment actually pulling upon the actual tie itself.
Given the danger and cost of the wall continuing to move after it has been supposedly re-tied, the client is paying to have the wall adeqautely re-tied together and not simply to have it drilled all over the the place so one may see how important such independent testing is to rule out such bad practice. Those who independently check should also sample check that ties have actually been installed to difficult to reach areas and that any existing ties of a type that should be removed have actually been done so.
See part 2 for continuation of subject matter:
Kindest regards to all,
David Aldred CSRT, AInstSSE, MIWSc, CSSW, Independent damp and timber surveyor0
This discussion has been closed.
Confirm your email address to Create Threads and Reply
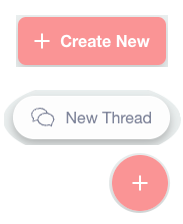
Categories
- All Categories
- 351.1K Banking & Borrowing
- 253.2K Reduce Debt & Boost Income
- 453.6K Spending & Discounts
- 244.1K Work, Benefits & Business
- 599.1K Mortgages, Homes & Bills
- 177K Life & Family
- 257.5K Travel & Transport
- 1.5M Hobbies & Leisure
- 16.1K Discuss & Feedback
- 37.6K Read-Only Boards