We'd like to remind Forumites to please avoid political debate on the Forum... Read More »
📨 Have you signed up to the Forum's new Email Digest yet? Get a selection of trending threads sent straight to your inbox daily, weekly or monthly!
rendered timber frame bay window
Options
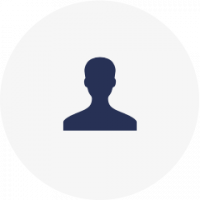
Tucker
Posts: 1,098 Forumite

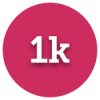
I have a timber framed bay window between the downstairs bay and upstairs bedroom bay, constructed in the early 90's.
I had the outside re-rendered this year as it had blown and cracked in several places after 20 years of weather on it. It had been badly done from day one with metal lattice that had rusted, and internal beading on the corners which had also degraded. At the same time, I removed the internal plasterboard which had a few small signs of moisture and found it was un-insulated. The only thing between the plasterboard and outside rendered plywood was damp proof membrane rolls laid overlapped, which was punctured in more places than I care to remember by nails holding on the board and the metal lattice.
I added 50mm of kingspan and left a 25mm air gap, re-boarded with vapour board and had it plastered.
The window was steaming up, so I lifted some floor boards and found the DPM beyond the air gap was wet. I could feel moisture beyond the kingspan, by sticking my hand up from below the joists. I took away some kingspan and cut through the dpm and found the ply beyond was dry, so the moisture is gathering from inside and wasn't getting in from outside. The render was done with 3 coats including a waterproof agent and sealed with dulux weathershield, so I am sure no moisture is coming in from outside.
I think I need to remove the plasterboard and kingspan and find a remedy. I need advice from anyone with experience of a timber frame construction?
My thoughts are to trim off any penetrating nails flush, apply a fresh layer of visqueen or breathable membrane?? Fill with fullfill insulation, add a further layer of visqueen and re-board with vapour board. I need to carry this down below the joists to where it meets the timber frame above the upvc window below.
Is there anyone familiar with rendered timber construction who can provide some advice?
I had the outside re-rendered this year as it had blown and cracked in several places after 20 years of weather on it. It had been badly done from day one with metal lattice that had rusted, and internal beading on the corners which had also degraded. At the same time, I removed the internal plasterboard which had a few small signs of moisture and found it was un-insulated. The only thing between the plasterboard and outside rendered plywood was damp proof membrane rolls laid overlapped, which was punctured in more places than I care to remember by nails holding on the board and the metal lattice.
I added 50mm of kingspan and left a 25mm air gap, re-boarded with vapour board and had it plastered.
The window was steaming up, so I lifted some floor boards and found the DPM beyond the air gap was wet. I could feel moisture beyond the kingspan, by sticking my hand up from below the joists. I took away some kingspan and cut through the dpm and found the ply beyond was dry, so the moisture is gathering from inside and wasn't getting in from outside. The render was done with 3 coats including a waterproof agent and sealed with dulux weathershield, so I am sure no moisture is coming in from outside.
I think I need to remove the plasterboard and kingspan and find a remedy. I need advice from anyone with experience of a timber frame construction?
My thoughts are to trim off any penetrating nails flush, apply a fresh layer of visqueen or breathable membrane?? Fill with fullfill insulation, add a further layer of visqueen and re-board with vapour board. I need to carry this down below the joists to where it meets the timber frame above the upvc window below.
Is there anyone familiar with rendered timber construction who can provide some advice?
0
Comments
-
try the forum on screwfix.com.....will probably get more help there0
-
Hi,
I think you have perhaps answered your own question really. If the outer cladding is dry and you have wetness on the cold side of the insulation the primary investigation once plumbing leaks have been ruled out would be interstitial condensation.
Please see http://www.basildon.gov.uk/CHttpHandler.ashx?id=1284&p=0
which is an illustration by Basildon Building Control that gives cross sections of insulated rendered timber framed walls (scroll down) amongst others and also please tel Kingspan advisory service on 0870 850 8333 who are very good and will probably send you a pdf file of typical cross section.
As an aside the hard dense cement renders are not particularly ideal despite what you will see in timber frame specifications because they are far less breathable than true lime renders. When cement render cracks it stays cracked allowing mosture to get behind and freeze / thaw action to spread the damage in addition to moisture ingress. It only requires a crack tothe render of 0.01mm to allow such moisture ingress. True lime renders are breathable and if they do suffer small cracks these tend to self heal as rainwater washes over them in the same way stalagmites are formed and this self healing does not happen with cement renders.
Hope this helps - kindest regards, David Aldred independent dampness and timber surveyor0 -
Thanks David
There's no pipework in the area, so it has to be condensation finding this area as it's probably the coldest surface.
What I have is very similar to the diagram, except there's no membrane between the ply and the EML / render as the vapour barrier has always been on the other side of the ply (punctured!!).
I can see what you mean with the render, as that's exactly what happened initially. The plasterers that made good felt it had gone wrong because the EML was poorly fixed and came off the board causing it to crack and then allow moisture in.
The render elsewhere - i.e. onto block has been fine, so it suggests the problem is the timber frame area.
If it goes again, I will certainly have a re-think and not repeat the process that way.
The true lime render sounds more suited to the ply, but would it marry up with the other rendered areas, which have a teraline finish?0 -
Oh, plan C was to clad the bay with upvc..... Not the best look by any stretch, but probably one which gives a sound barrier against water penetration and something within the skills of a DIYer like me.0
-
Hi again Tucker,
The things to bear in mind with framed walls suffering interstitial condensation are an effective vapour barrier on the back of the plasterboard and indeed all areas throughout including perimeter and service interfaces that is fully taped / adhesive sealed to prevent warm moist air from the room entering the void and if necessary adequate ventilation externally on the cold side of the insulation to remove any moisture laden air attempting to condense. You have insulated the void with the best of intentions but you are likely to have made the void that remains beyond the partial fill insulation colder as a result and therefore more prone to interstitial condensation. Please be aware that it only takes a small area where there is an inadequate vapour control to allow warm moist air from the room to get into and beyond the insulation by whatever tortuous path it chooses it will occur given it is a gas. I have seen this fault occur at perimeters such as floor / intersecting walls and ceilings and also where services penetrate the system such as plug sockets / water pipes etc. You also need to ensure that the insulation itself is absolutely continuous and of uniform thickness throughout with taped joints throughout to all areas because if you omitted the smallest bit you will have created a cold spot prone to chronic condensation that may be even more acute in this area than prior to you insulating it. General use plasterboard without a foil backing will allow moisture to permeate through it so foil backed boards are required which may also have to be fire rated in certain applications. If you were changing to cladding please check that your Local Authority Planning department has no objections and consult your Local Authority Building Control Dept for a detailed specification that they propose for both your existing construction and any proposed alterations such as cladding.
Hope these general principle comments help - David Aldred independent dampness and timber surveyor.0 -
Thanks, they very much do.
Yes I put in the 50mm kingspan thinking it was a big impovement, but clearly I've made the remaining 25mm void that much colder than it was before and therefore worse than when it was un-insulated!!
I am going to remove the foil board and kingspan and do it again, renewing the dpm where needed to make it air tight, filling the void fully probably with drytherm cavity fill, then a further layer of dpm and new foil backed board. Below the joists I'll use ply instead of the plasterboard and seal with silicone / jointing tape to stop any moisture getting into the area.
Double checked the render tonight and it's perfect.0 -
Update - Looks like my diagnosis wasn't quite right....
Ripped off the Foil board and removed the Kingspan. Whilst they were both dry, the DPM was very wet beyond it on the inside and it appears water has been getting in under the window sill from outside and running down the inside of the membrane!
I've now silcone sealed the underneath of the outside sill and hopefully made it water tight. Once I'm sure it's keeping the rain out, I'll do a better job of the inside and 'hopefully' not have to rip it out ever again!0 -
Had this done a few months back the original was timber over very thin fibreglass insulation and damp. I didn't want timber again and hate pvcu Stone effect insulation boards are poly something or other,about 21/2" thick over roof membrane
.http://www.flickr.com/photos/35286279@N05/4106337261/
Looks real and all damp has now gone and internal walls seem warmer to touch.0 -
Have you done it yourself or had someone in?
My biggest problem is that all the houses on the close have the same render finish, so doing anything radical will probably look out of place.0
This discussion has been closed.
Confirm your email address to Create Threads and Reply
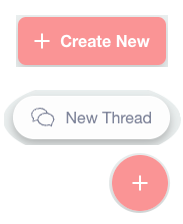
Categories
- All Categories
- 351.1K Banking & Borrowing
- 253.2K Reduce Debt & Boost Income
- 453.6K Spending & Discounts
- 244.1K Work, Benefits & Business
- 599.1K Mortgages, Homes & Bills
- 177K Life & Family
- 257.4K Travel & Transport
- 1.5M Hobbies & Leisure
- 16.1K Discuss & Feedback
- 37.6K Read-Only Boards