We'd like to remind Forumites to please avoid political debate on the Forum... Read More »
📨 Have you signed up to the Forum's new Email Digest yet? Get a selection of trending threads sent straight to your inbox daily, weekly or monthly!
Cold bridging?
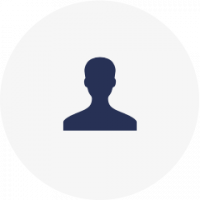
princessamy86
Posts: 4,889 Forumite
Hi all
I had a cavity wall insulation surveyor round today and he has said that under NO circumstances should I get it installed as we have cold bridging in 3 spots? Now I know what cold bridging is, but I have no idea how it's put right. We have terrible condensation problems and I thought the insulation would help with this, but apparently not! I'm going to get a survey off a local damp specialist company, but as they have a vested interest I would be grateful if anyone on here could help me with what to expect. We already do the whole stopping condensation rigmarole, windows open, don't air dry washing, have the heating on, have a de-humidifier, but it doesn't stop it. Any suggestions gratefully received!
I had a cavity wall insulation surveyor round today and he has said that under NO circumstances should I get it installed as we have cold bridging in 3 spots? Now I know what cold bridging is, but I have no idea how it's put right. We have terrible condensation problems and I thought the insulation would help with this, but apparently not! I'm going to get a survey off a local damp specialist company, but as they have a vested interest I would be grateful if anyone on here could help me with what to expect. We already do the whole stopping condensation rigmarole, windows open, don't air dry washing, have the heating on, have a de-humidifier, but it doesn't stop it. Any suggestions gratefully received!
Scar tissue that I wish you saw, sarcastic mister know it all, close your eyes and I'll kiss you cause with the birds I'll share this lonely view.
0
Comments
-
Have you asked the cavity insulation company what they mean by cold bridging and more importantly where it is. I think also that I would want them to tell me how they came to this conclusion. If you do not know where this 'cold bridging ' is occurring, How is it possible, even to begin to work out a way of sorting it. I think that I would be getting another survey from a different company before I made any decisions on the subject.I can afford anything that I want.
Just so long as I don't want much.0 -
I wasn't in, it was my OH and I'm absolutely gutted that I wasn't there as I would have asked a lot of questions! I'm definitely going to get another survey done, it's just obviously the cost and the potential that it may not be fixable. As I understand it, cold bridging occurs across wall ties and creates cold spots which leech water and create damp and mould. Do you think a damp specialist surveyor is the way forward? Or should it be a different type?Scar tissue that I wish you saw, sarcastic mister know it all, close your eyes and I'll kiss you cause with the birds I'll share this lonely view.0
-
Hi Princessamy,
The following is a bit long winded and is given in good faith as general comments only. Specific cases may well vary but hope it is of some use to you.
Installing cavity wall insulation to properties that are already built is a bit of a hot potato. The government and many people quite rightly want to cut down fuel costs and improving the insulation to walls is a method of achieving this and within that there are options of improving insulation internally within the rooms themselves by insulated dry linings and other means, alternatively to insulate the cavity voids within cavity wall type constructed wall and again alternatively to insulate the outside of the building by such means as insulated render and other systems. Each has its advantages and disadvantages but it is perhaps the cavity wall insulation that gets most of the attention and there are just as many people for it as there are against it. Out of all the ways to insulate the walls it is often the cheapest, there are grants for it, it requires no external or internal changes, is often done in a day and is not seen other than making good of drill holes where it is installed.
In the case of cavity wall insulation there are things that should be considered before having it undertaken if that is the method you want to use to improve the wall insulation. When a person has inspected a property to see if that property is suitable for cavity wall insulation they would do well to have complied with British Standard BS8208 which ran from 1985 until 1st July 2009 when it was withdrawn. The main thrust of this document with regard to inspection was is if the property was inappropriate for such insulation by way of its location, construction, the cavity wall was of inadequate width, or was compromised, or there were existing issues of dampness, then to recommend the insulation not be installed, at least until such issues could be addressed if possible to do so.
In this case your cavity wall insulation surveyor has noted areas of concern and said the wall is currently unsuitable so well done to them for their honesty as some installers seem to put the insulation into the most unsuitable properties.
There are several different types of cavity wall insulation on the market and from personal experience of looking into cavity walls for a living, some types of insulation seem to be less problematic than others. Anyone who watched the BBC program The One Show the other week will have seen the wet cavity wall insulation being removed like a saturated mass from the base of walls and when this happens it can cause havoc internally with dampness, mould, degraded plaster and finishes in addition to accelerating ferrous type cavity wall tie corrosion (cavity wall ties are what holds the inner leaf of the cavity wall to the external leaf and gives it the required structural stability). If ties fail through corrosion there is nothing to hold the outer leaf of the wall on and it has been known to collapse suddenly and dramatically usually in high winds through a pumping action though such instances are fortunately not common.
Installing the cavity wall insulation to existing properties is done blindly usually from the outside which is far different from putting the insulation into the wall carefully as it is built with new construction. The result of such blind insulation to existing properties is that sometimes the insulation does not go everywhere it is supposed to and voids occur. Where there are voids there are cold spots on the wall and the dew point (the temperature at which condensation will occur for a certain temperature) can be reached at these points. In addition some types of insulation slump over time again creating voids. If there is debris within the base of the cavity wall this will allow dampness to rise up through it and give all the effects of rising dampness whether or not the damp proof course in the brickwork of the wall is effective or not and allow dampness to strike across the wall. Such debris will also cause cold bridging making the area prone to condensation both on surfaces and within the depth of the wall itself (the latter being called interstitial condensation). If such debris is not removed from the base of the cavity of the wall (or anywhere higher up the wall where it may have lodged) before the wall is cavity wall insulated then the insulation will not be present to such areas and they will be colder than the insulated areas and prone to condensation. The pores in the masonry are meant to contain air. If they contain moisture they are colder and more prone to condensation which can be a downward cycle that becomes progressively more widespread until a moisture resevoir develops that sustains the dampness through more favourable weather.
If there are issues of corrosion to existing cavity wall ties or inadeqaute number of cavity wall ties to comply with the Building Regulations then the cavity wall ties should be addressed before the wall is considered for suitability for cavity insulation. The reason for this proposal is that once cavity wall insulation is installed then the process of addressing cavity wall ties afterwards can be a nightmare. This is because installing cavity wall ties is done by hammer drilling into both the inner and outer leaf of the cavity wall and as this is done it causes the back of the brick to break away and debris to fall into the cavity. Normally this debris should be removed from the base of the cavity wall after the ties have been installed. However once insulated if wall tie work is then carried out such debris would simply sit upon the insulation at each and every point where new ties had caused such debris to fall and if sufficient can quite easily bridge the cavity allowing penetrating dampness and condensate to enter the inner leaf of the wall and then into the room causing damp / mould / degraded plaster / disrupted finishes.
To make the hassle even worse some types of original cavity wall ties if large in section should be either removed or isolated from the wall as when they expand with corrosion they will crack the surrounding mortar beds. Mortar is strong in compression but weak in tension. Repeated cracks up the entire height of a wall where there is an expanding corroding cavity wall tie creates enough forces to put walls out of alignment and lift roofs as the effect is cumlative. As you might imagine opening a cavity wall up to remove or isolate each original cavity wall tie means you will allow the cavity wall insulation to fall / spill out of the wall and you can empty a wall of isnulation if you don't stop it falling out if it is a loose type, or at the very least you will have to attempt to try and make it good in each and every place you disturb it with accessing original cavity wall ties.
It should also be appreciated how the moisture dynamics of the wall are affected by putting cavity wall insulation into existing properties. If the cavity is clear as it was built then air moves freely within the cavity drying out any moisture penetrating the outer leaf of the cavity wall. The amount of moisture that will come through the half brick thick outer leaf of the cavity wall subjected to prolonged wind driven rain shoudl not be under-estimated. The inside face of the outer leaf of the cavity wall can get very wet indeed and all remains well if it is seperated from the inner leaf / internal rooms. When insulated the condensate within the cavity can be considerable on the cold side of the insulation when you have a room at a comfortable temperature with warm moist air in it and an outside temperature that is a lot lower. When fully filled with insulation air movement within the cavity does not stop but it is significantly reduced and there will be a consequential increase in condensation problems within the depth of the wall itself when you create such a semi closed enviroment.
Where any moisture within the cavity be that penetrating dampness or condensate could trickle down the cavity to the base of the wall prior to it being insulated this process does not stop but again the speed at which this occurs reduces significantly and with it the tendancy for the insulation and cavity as a whole to become a saturated mass.
If older properties have been cement rendered or just cement mortar re-pointed instead of the breathable renders and mortars they were built with then these hard dense cement based materials reduce evaporation outwards compared to the original breathable renders and mortar such as true lime based. This impacts when cavity wall insulated because the condensation and penetrating dampness issues described above do not as readily evaporate outwards under such circumstances and take the easier more permeable route of going inwards to rooms etc. The same will apply when an outer leaf is hard dense facing brick compared with more porous clay inner brickwork or blockwork. The problem can even be made worse where the sun shines for long periods upon such cement rendered/ cement re-pointed elevations as the sun can actually drive such moisture into the fabric of the building, rather than as you might think evaporate it outwards.
When condensate and penetrate dampness comes down the cavity it has two options when it comes across lintels, cavity wall ties and the base of walls or other obstructions. What you want is for such moisture to drain outwards but if there is no pathway for this to occur such as via weep joints in the outer leaf of the cavity wall it is going to take the easier route and migrate inwards. If there is debris upon ties, and / or the tie is incorrectly sloping down towards the inner leaf of the wall the moisture will run across and inwards. If there is debris sat upon lintels as often is the case, the moisture will track inwards and when it hits the base of the wall the moisture will run inwards. Also be mindful that many old porous stone window cills are built all the way across the cavity wall to the back of the plaster which makes this area unable to be insulated, prone to penetrating dampness and a chronic cold spot prone to condensation / associated mould growth.
As you might imagine many cavities are far from perfect and there are mortar droppings and considerable debris within them. In some areas such as where I live near to the coast, sand is in the air for quite a few miles inland and you might not think so but it enters the cavities to walls and swirls around eroding the brickwork inside and any hidden faces feature stone from the inside which turns to dust and impacts the cavity. Many cavities are less than the minimum width of 50mm recommended for cavity wall insulation especially where compromised.
The cavity wall insulation should not be installed to properties which are classed as subject to severe exposure. The last time I spoke to the BRE they said any property within 8km of the sea is classed as severe exposure in addition to those which are exposed due to being on hills and above surrounding properties etc. Maps are available showing areas subject to severe exposure within the Building Regulations which can be accessed online and also within BS5535 and looking at these you can see that generally most of the left hand side of the country, wales and most of scotland are classed as severe exposure on these maps.
Also be mindful that the damp proof course the house was built with may project into the cavity by a few milimetres and act as a ledge to catch not only the debris mentioned above but also penetrating dampness and condensation then direct such moisture in towards the property.
Be mindful also that the void beneath any suspended timber ground floors needs to be adequately ventilated if the floor is not to suffer rot. The cavity wall insulation installer should really, as part of their pre-installation survey, look at the moisture content of any suspended timber ground floor, recommend opening up the floor for further inspection if they are alerted by high moisture readings and halt any proposed cavity wall insulation. If such moisture readings are acceptable remove existing terracota or plastic sub floor vents and dam the cavity within the wall round the vent with suitable material to prevent the cavity wall insulation falling into the vent area and compromising it.
This work is often done with flexible brushes forced into the cavity of the wall around the vent but I have known installers take out vents and put vents back without such intalling dams simply because they had forgot to put them on the van or ran out of them when doing the job. The consequence of this has been the ventilation to the sub floor is reduced or stopped by the insulation and the floor begins to decay when its moisture content consequentially rises above the threshold of decay (20-22%).
There are claims I have read that around 40% of houses that are attempted to be cavity wall insulated after they were built have increased dampness problems. I cannot back this figure up but I can say that where I live near the coast the problems of wet cavity wall insulation, chronic levels of voids to cavity wall insulation and consequential internal dampness are common with properties I inspect on a day in day out basis. The most common insulation material I see as a wet mass is the blown fibre type. The most common insulation that has flowed out onto sub floor voids is the loose poly ball / chips. The expanding foam I see cracks to it causing in effect channels for moisture to track down and into the rooms.
Where cavities are perfect, they are wide enough, the property is not exposed to severe weather, cavity wall ties are free of corrosion, the external leaf of the cavity wall is breathable and sub floor ventilation not compromised in any way, then the system may be worth considering along with the other possibilities.
Where the cavity wall insulation is found to be compounding dampness the insulation material can be removed but this is not easy requiring scaffolding of elevations and then brick and where applicable render removal plus all the making good. The loose fill material and blown fibre material I have seen being sucked / blown out through access holes cut into the wall to remove the product.
Cavity wall insulation is put into new build properties and the best way of doing this I have seen is where the cavity is wider then the 50mm or less found in older proeprties by making it around 100mm wide but the 50mm wide insulation is then held back to the inner leaf of the cavity wall with special ties taking up 50mm of that cavity width and leaving 50mm clear void to reduce the issues described above.
Insulated dry linings / cavity wall insulation / external insulated renders / panels - you pays your money (and so do the government with subsidies to such schemes) and you takes your choice.
Endoscope photographs available upon request of issues discussed.
P.S. If you are having cavity wall insulation also check the mains electrical wiring has not been run down within the cavities of the wall as some electricains have a habbit of doing. The saturated environment compounded by the insulation due to reaons discussed above within the cavity can find any weaknesses in such wiring especially if those drilling the walls all over the place to install the insulation / cavity wall ties have not spotted the cables and caught the outer sheathing or worse within with their drills. Suddenly you start blowing fuses / tripping the circuit breakers and don't know why - finding such an electical fault in amongst that insulation is then a bit of a nightmare.
Hope this general info helps, Kindest regards David Aldred independent dampness and timber surveyor0 -
This seems to be more of an encyclopedia than a post. I hope that you pasted it rather than typed it.I can afford anything that I want.
Just so long as I don't want much.0 -
Prize for longest post ever goes to David Aldred! :beer:Everything that is supposed to be in heaven is already here on earth.
0 -
But boy, is it enlightening!:T0
-
Sorry I know it was a hell of a long read but there was a lot of issues in there and no I didn't cut paste just hammered it out on the keyboard - obviously too much time on my hands (laughing). I have just gone back to it and added a section at the end regarding the electrical wiring installation and how this may be compromised by cavity wall insulation / wall tie issues during installation. Kindest regards to all, Dave Aldred0
-
Thanks very much David, it was certainly an enlightening read! Still not really sure what I should do? Any recommendations? You could come and have a look if you like, I'm not so far from Cleveleys
!
Scar tissue that I wish you saw, sarcastic mister know it all, close your eyes and I'll kiss you cause with the birds I'll share this lonely view.0 -
The thing to bear in mind is that getting insulation fitted will not necessarily solve your condensation problem,
Davids post whilst long is very factual
As a 'damproofing' surveyor I am mindful that people are wary that we have a 'vested' interest, HOWEVER the thing to bear in mind is that, the right surveyors vested interest is giving you a solution to your problem.
You have 3 cold spots - big deal! what about the rest of the property that hasn't got these 'cold spots' ?? Most houses will have cold spots if you look for them!
You should consider getting a positive ventilation unit fitted, these units will treat your condensation problem at source AND if the condensation problem is under control the 3 cold spots won't be such an issue.
Consider one of the Nuaire Drimaster systems, the envirovent loft unit (assuming you have a loft space) there are other out there but these 2 companies are the major players.
It's always difficult without actually seeing your property, but my thoughts are to consider
1. Fitting a PIV unit
2. Get your cavity wall insulation fitted
3. Live happily ever after
www.nuaire.co.uk
www.envirovent.com
Nuaire will supply direct, not sure about envirovent as I'm a trade user
Other nuaire suppliers are out there just google 'drimaster'
I have a favourite I use all the time, Pm me if you want the link as I don't want to keep advertising them and be accused of spamming)
Hope this helps
DDThe advice I give on here is based on my many years in the preservation industry. I choose to remain anonymous, I have no desire to get work from anyone. No one can give 100% accurate advice on a forum if I get it wrong you'll get a sincere apology and that's all:D
Don't like what I have to say? Call me on 0800 KMA;)1 -
I'm worried about the cold bridging because we only had the wall ties done last year, so hopefully that doesn't mean they've mucked it up. I'll have a look at those links Dave, thanks very much and have sent you a PM.Scar tissue that I wish you saw, sarcastic mister know it all, close your eyes and I'll kiss you cause with the birds I'll share this lonely view.0
This discussion has been closed.
Confirm your email address to Create Threads and Reply
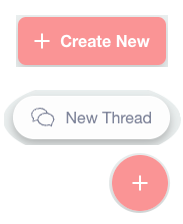
Categories
- All Categories
- 351.3K Banking & Borrowing
- 253.2K Reduce Debt & Boost Income
- 453.7K Spending & Discounts
- 244.3K Work, Benefits & Business
- 599.5K Mortgages, Homes & Bills
- 177.1K Life & Family
- 257.8K Travel & Transport
- 1.5M Hobbies & Leisure
- 16.2K Discuss & Feedback
- 37.6K Read-Only Boards